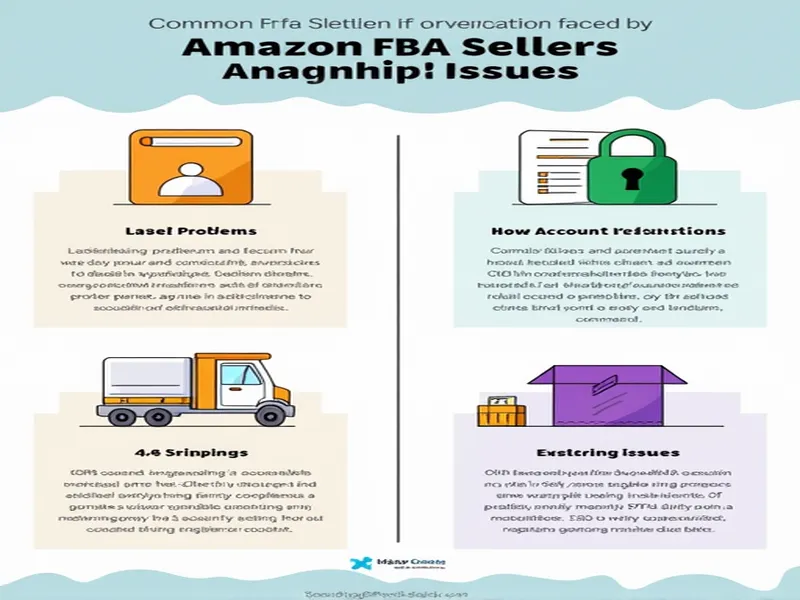
In today's rapidly evolving e-commerce landscape, Amazon's Fulfillment by Amazon (FBA) program has emerged as a popular logistics solution attracting an increasing number of sellers. However, operational challenges frequently arise. This article explores practical solutions to common FBA issues, helping sellers optimize their business operations, boost sales, and enhance customer satisfaction.
1. Missing Shipping Labels
Properly affixed shipping labels are critical when sending inventory to Amazon's fulfillment centers. If labels are forgotten, sellers should immediately contact Amazon support to determine if relabeling is possible. While missing labels won't directly impact seller accounts, they can delay product availability. Providing shipment details like batch numbers typically facilitates resolution.
2. Account Restrictions
When facing account limitations while having inventory in FBA warehouses, sellers might consider using another unrestricted account. However, Amazon's strict policy against account association requires careful management to avoid both accounts being suspended. A safer approach involves transferring inventory to third-party warehouses for relabeling before returning to FBA, ensuring consistent SKU and label information.
3. Origin Label Accuracy
FBA automatically generates shipping origin information on labels, which cannot be modified post-generation. Sellers must verify all origin details during label creation, preparing accurate shipping documents beforehand to prevent logistical complications.
4. Barcode Management
Effective barcode usage is essential, with FNSKU (Fulfillment Network Stock Keeping Unit) being Amazon's recommended compliant option. For scanning issues, sellers should:
- Ensure barcode print quality
- Regularly maintain scanning equipment
- Verify device calibration
5. Labeling Errors
Discovered label mistakes require immediate action—contact freight forwarders for relabeling before warehouse receipt. Amazon systems may flag incorrect labels, potentially causing inventory issues. Implementing pre-shipment verification processes minimizes such errors.
6. New Product Visibility
When new ASINs (Amazon Standard Identification Numbers) aren't searchable, sellers should:
- Confirm correct FNSKU usage
- Verify listing information accuracy
- Check Seller Central for required adjustments
7. Label Optimization
While minimal labels (barcode + FNSKU) are functional, adding product names enhances warehouse efficiency and customer experience. Clear product identification aids market visibility in competitive environments.
8. UPC Label Updates
When prompted to replace existing UPC labels with FBA labels, sellers can adjust settings via Seller Central or recreate listings with proper labeling standards. Maintaining clear UPC/FNSKU records ensures efficient management.
9. Container Labeling
Proper labeling differs by container size:
- Individual product labels for small boxes
- Master labels for large containers
Consolidated shipments through bundled accounts can reduce transportation costs.
10. Barcode Selection
FNSKU remains Amazon's preferred labeling method, directly linking to FBA inventory. While EAN barcodes have situational use, FNSKU consistency improves operational efficiency and reduces errors.
11. Unlabeled Shipments
For shipped items lacking labels, immediate Amazon support contact is crucial to prevent inventory or sales delays. Pre-shipment label verification processes help avoid recurrence.
12. Weight Compliance
Amazon enforces strict weight limits (22.7kg/50lbs per box). Clear weight labeling prevents handling errors during unloading and weighing.
13. Listing Restoration
Accidentally deleted listings can be reconnected to inventory using original SKUs through seller support. Maintaining SKU consistency across sales channels prevents similar issues.
14. Duplicate FBA Plans
Repeated FBA plan creation doesn't alter product labels. Sellers can continue using existing labels, simplifying inventory tracking when maintaining uniform SKUs.
15. Container Size Discrepancies
When actual container dimensions differ from system settings, sellers must decide whether relabeling is necessary. Regular communication with logistics partners and standardized shipping practices prevent such issues.
16. Color Label Accuracy
Using FNSKU for product identification minimizes mislabeling. Including product attribute descriptions in packaging further prevents confusion during fulfillment.
17. Inventory Tracking
Seller Central's display options allow viewing product-FNSKU relationships, enabling effective inventory management. Regular product audits identify potential issues early, reducing operational costs.
By understanding and addressing these operational challenges, Amazon FBA sellers can optimize their business performance, enhance market competitiveness, and improve customer satisfaction—key factors for sustainable e-commerce success.