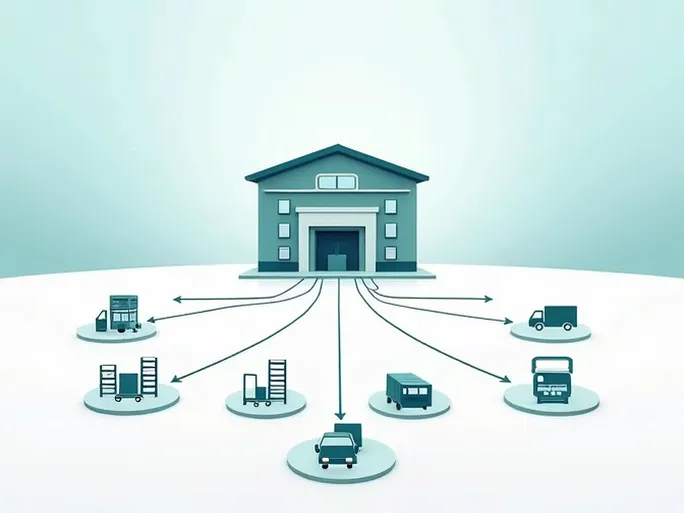
In today's rapidly evolving business landscape, efficiency and accuracy have become critical components of effective warehouse management. Companies face increasingly intense market competition, while customer demands for variety and personalization add complexity to supply chain operations. In this context, optimizing warehouse processes can significantly reduce operational costs, improve efficiency, and enhance customer satisfaction and loyalty.
I. Fundamental Concepts of Warehouse Processes
1. Defining Warehouse Processes
A warehouse process is a multi-stage system that manages goods from receiving through to shipping. This workflow encompasses receiving, storage, picking, packing, and shipping operations. The process must address both the physical movement of goods and the flow of information while optimizing resource allocation. When designing or improving warehouse processes, it's essential to understand the interrelationships between different stages and how information technology can enhance overall operational efficiency.
2. Key Components
An efficient warehouse process typically includes these core components, each directly impacting overall performance:
- Receiving: The starting point of warehouse operations involves inspecting and recording incoming goods while planning optimal storage locations. Technologies like barcode scanning, RFID, and EDI can significantly improve information processing efficiency and reduce human errors.
- Storage: Warehouse storage capacity directly affects inventory management flexibility and space utilization. Implementing appropriate storage solutions (racks, automated warehouses) and using software systems for real-time inventory monitoring maximizes space usage while improving retrieval efficiency.
- Picking: This stage critically impacts order processing and customer service efficiency. Businesses should select picking strategies (single-order, batch, or wave picking) based on operational needs, optimizing task sequences and routes to minimize time and costs.
- Shipping: The goal is accurate, error-free delivery to customers. Strict packaging standards and loading procedures, combined with barcode/RFID tracking, help minimize shipping mistakes.
II. Process Planning Steps
Warehouse process optimization requires several essential steps, each based on thorough data analysis and market research.
1. Demand Analysis
The foundation of warehouse planning begins with understanding customer needs and market trends to forecast inventory requirements. Analyzing historical sales data, market research, and industry trends helps identify product categories, sales fluctuations, and seasonal demand patterns. Data accuracy is paramount, and analytical tools can improve forecasting reliability.
2. Process Design
After demand analysis, companies can develop operational plans. Effective process design should be visual, typically presented as flowcharts showing workflow sequences, handoff points, and information pathways. Streamlined designs minimize unnecessary product movement and enhance operational efficiency.
3. Resource Allocation
This involves optimal distribution of personnel and equipment. Workforce allocation should match operational requirements at each process stage, while equipment selection depends on process design and product characteristics. Automation can dramatically improve efficiency while reducing labor costs.
III. Key Technologies and Tools
Technological advancements have introduced numerous innovations to warehouse management, improving both efficiency and operational flexibility.
1. Warehouse Management Systems (WMS)
WMS serves as the operational control center for daily warehouse activities. These systems enable real-time inventory monitoring, ensuring smooth workflow transitions. Advanced WMS solutions can intelligently manage picking operations by automatically generating picking plans and optimizing routes based on inventory status and customer demand, significantly reducing order processing times.
2. Automation Equipment
Automated solutions like AGVs (Automated Guided Vehicles) and automated picking systems are becoming standard in modern warehouses. These technologies dramatically improve accuracy and throughput while reducing labor requirements, enabling cost-effective handling of peak demand periods and market fluctuations.
3. Data Analytics and Optimization Tools
Analytical tools support demand forecasting and inventory management through data-driven decision making. Implementing such systems increases process transparency while continuous monitoring identifies improvement opportunities for ongoing optimization.
IV. Evaluation and Continuous Improvement
Ongoing process evaluation ensures warehouse operations meet performance targets. Two primary assessment methods include:
1. Key Performance Indicators (KPIs)
Quantifiable metrics like picking accuracy, inventory turnover, and order processing time provide clear visibility into warehouse performance. For instance, achieving >95% picking accuracy typically correlates with reduced customer complaints and higher satisfaction.
2. Continuous Improvement Methodology
Lean management principles help systematically identify and eliminate supply chain waste. Regular equipment maintenance, process optimization, and PDCA (Plan-Do-Check-Act) cycles ensure sustainable improvements.
Conclusion
Scientific warehouse process planning and management enable companies to significantly enhance operational efficiency while adapting to dynamic market demands, supporting sustainable business growth. This capability represents a critical competitive advantage in today's marketplace.
Looking ahead, digitalization and intelligent automation will become indispensable to warehouse management. Forward-thinking organizations must continuously monitor technological innovations and process optimization opportunities to maintain their competitive edge.