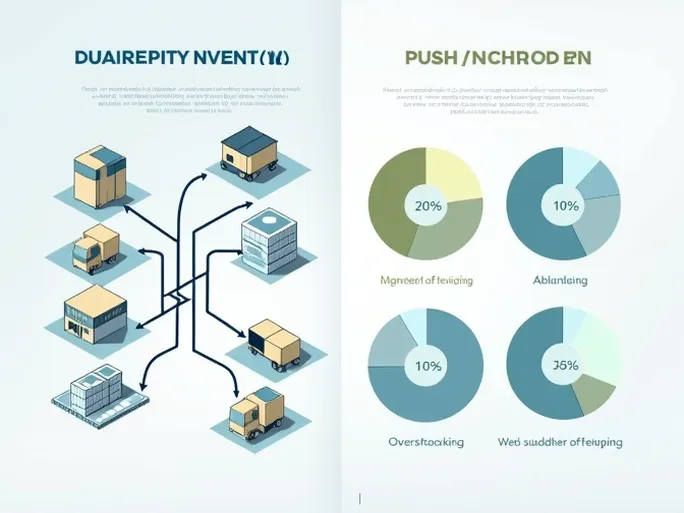
In today's rapidly changing market environment, the importance of inventory management has become increasingly prominent. Businesses require efficient inventory strategies to respond to fluctuating demand while reducing inventory costs. Push inventory management, as an effective strategy, is being adopted by more and more enterprises. It not only optimizes resource allocation within supply chains but also effectively balances inventory and demand.
The Fundamentals of Push Inventory Management
Push inventory management is a replenishment strategy based on demand forecasting, determining inventory levels by considering orders from downstream businesses and production capacity. The core of this model lies in achieving rational resource allocation between various storage points, ensuring optimal balance between production efficiency and inventory costs.
Preparations for Implementing Push Inventory Management
Before implementing push inventory management, several key questions must be addressed:
- What inventory levels should be maintained at each storage point?
- How should each production batch be allocated across storage points?
- How should excess production capacity and inventory be reasonably distributed among storage points?
Calculation Steps for the Push Management Model
After clarifying these questions, businesses can follow these steps for push inventory management calculations:
- Market demand forecasting: Analyze average demand between production batches.
- Current inventory audit: Document current inventory levels at each storage point.
- Determine safety stock levels: Calculate using the formula: Safety stock = Forecast error × Z cumulative probability distribution value.
- Calculate total demand: Total demand = Average demand + Safety stock.
- Determine net demand: Subtract current inventory from total demand to obtain net demand.
- Product allocation strategy: Distribute additional products based on demand forecasts using the formula: (Average demand a / Total average demand (a+b)) × Additional product quantity.
- Allocate total products to storage points: = Net demand + Allocation quantity.
Implementation Process of Push Inventory Management
The general steps for effective push inventory management implementation include:
- Aggregate all orders from subordinate businesses to calculate total order quantity.
- During production, if demand is met, distribute surplus according to order proportions to downstream businesses; otherwise, record shortages proportionally.
Push vs. Pull Inventory Management: A Comparative Analysis
Push and pull inventory management each have distinct advantages and disadvantages. Pull management emphasizes replenishment based on specific needs, typically responding to immediate warehouse demand. However, this approach may lead to poor overall coordination and ineffective synchronization of production batches and replenishment timing.
In contrast, push inventory management utilizes historical data and market trends to coordinate across storage points comprehensively, ensuring optimal balance between production scale economies and safety stock. This method is particularly suitable for businesses where production quantities significantly exceed short-term demand.
When designing inventory management strategies, businesses must consider multiple factors including sales data, storage capacity, and overall market trends. Through synchronized decision-making across storage points, push inventory management can enhance service levels while reducing unnecessary inventory accumulation and costs.
Conclusion
In modern supply chain management, push inventory management provides enterprises with an efficient approach to inventory control, helping them maintain competitiveness in dynamic markets. Selecting the appropriate inventory management model can yield significant cost savings and operational improvements.
Effective inventory management extends beyond mere stock control—it represents the embodiment of intelligent decision-making and precise analysis. By understanding and applying both push and pull models, businesses can achieve optimal inventory configuration and attain higher operational efficiency.