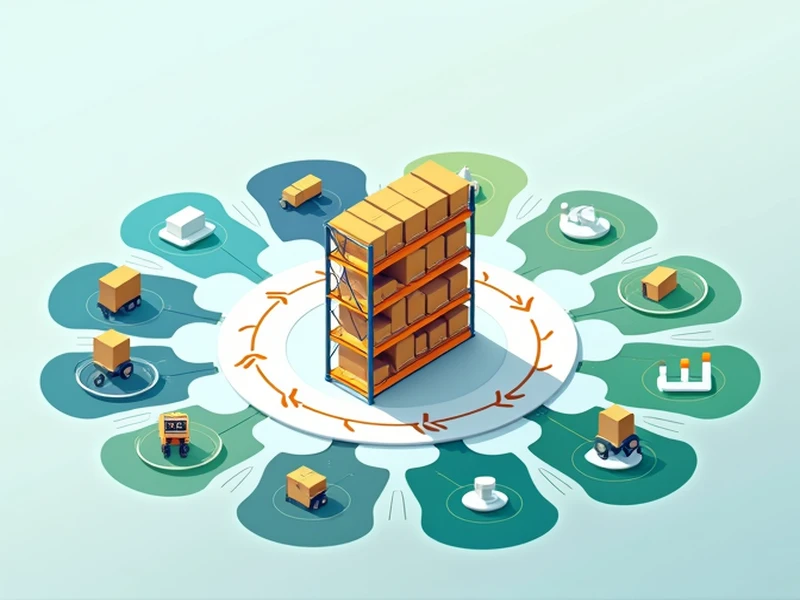
As market competition intensifies and consumer demands for timely delivery and service quality escalate, traditional warehouse management approaches reveal their limitations. This necessitates a paradigm shift toward lean management principles to break through conventional models and substantially enhance warehouse efficiency.
First, we must recognize that traditional warehouse management often relies on fixed inventory levels and simplistic processes, operating under the outdated assumption that "more inventory means less risk." However, this mindset fails to meet modern market requirements, frequently resulting in wasted storage space, inventory pileups, and even obsolescence of unsold goods. We must now understand that warehouse management transcends mere item storage and handling - it serves as a vital interface between enterprises and dynamic market forces.
The lean management philosophy has consequently gained traction among forward-thinking organizations. It emphasizes waste reduction, process optimization, and precise demand forecasting to elevate overall warehouse performance. This innovative approach provides businesses with more efficient and flexible solutions, transforming warehouse operations into smarter, more refined systems.
The core principle of lean management is "maximizing value while minimizing waste." In practical terms, every operational and logistical process should focus on creating greater customer value while eliminating unnecessary resource expenditure. Implementation requires translating this philosophy into actionable methodologies that deliver measurable results.
Practical Applications of Lean Warehouse Management
In practice, lean warehouse management demands meticulous optimization across multiple dimensions - from overall layout and inventory control to technological implementation. Below we examine several key methodologies that enable continuous improvement in warehouse efficiency and waste reduction.
1. Warehouse Layout Optimization: Minimizing Unnecessary Movement
Layout optimization constitutes the foundational step in lean warehouse management. A rational design not only improves spatial efficiency but also reduces redundant employee movement, thereby boosting productivity.
- Strategic Placement of High-Turnover Items : Storage locations should reflect product velocity, with frequently picked items positioned near picking zones to minimize retrieval time and unnecessary travel.
- Precision in Pathway Design : Warehouse pathways directly impact worker efficiency. Well-planned aisles prevent employees from traversing nonessential areas, reducing time waste.
- Maximizing Vertical Space Utilization : Implementing high-density storage systems and vertical racking eliminates spatial waste while increasing storage capacity.
2. Precision Inventory Management: Dynamic Optimization
Lean management's "just-in-time" production principle applies equally to warehouse operations. Accurate inventory control prevents stockpiling while ensuring smooth product flow and cost reduction.
- Advanced Demand Forecasting : Modern warehouses leverage big data analytics and machine learning to predict inventory needs based on market trends and seasonal fluctuations, preventing both shortages and surpluses.
- JIT (Just-In-Time) Implementation : This philosophy emphasizes meeting production and sales demands with minimal inventory at precisely the right time, optimizing capital efficiency.
3. Digitalization and Automation Technologies
- Warehouse Management Systems (WMS) : These core systems provide real-time monitoring of storage and movement, enhancing inventory control.
- Barcode & RFID Technology : Enables precise item tracking with real-time inventory updates, improving accuracy while reducing labor costs.
- Automated Equipment : Automated picking and handling systems decrease manual operations while increasing speed and precision.
Critical Success Factors
Three strategic elements prove indispensable for successful lean warehouse implementation: accurate demand forecasting, process standardization, and cross-departmental collaboration.
- Precision Forecasting : The cornerstone of warehouse management, enabled by data analytics for dynamic inventory adjustment.
- Standardized Processes : Eliminates operational variability through consistent, clearly defined workflows.
- Interdepartmental Coordination : Supply chain optimization requires seamless cooperation between procurement, sales, and logistics for shared visibility and decision-making.
Measurable Benefits
Lean warehouse management delivers tangible improvements in operational efficiency and customer satisfaction.
- Enhanced Operational Efficiency : Streamlined processes and automation reduce redundant steps, accelerating throughput while lowering costs.
- Elevated Customer Satisfaction : Precise inventory control and efficient distribution improve service quality, strengthening brand loyalty.
Lean warehouse management represents more than operational refinement - it serves as a strategic weapon for navigating market challenges. We must consistently apply these principles to maintain efficiency and sustain competitive advantage.