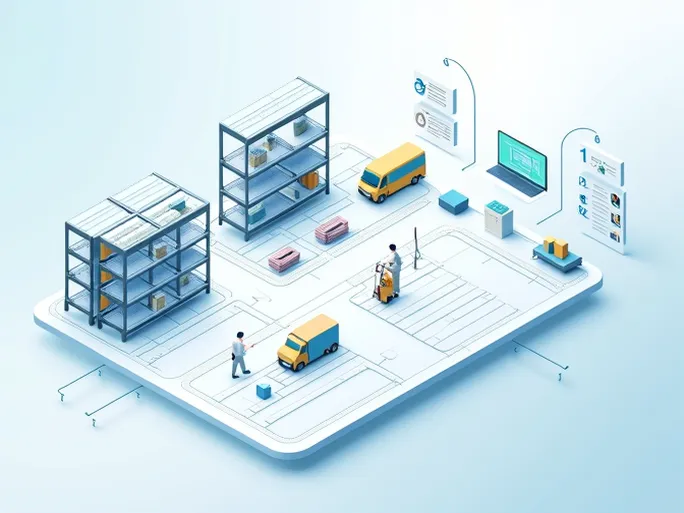
In modern logistics management, warehouse operational efficiency plays a crucial role in distributor success. However, many distributors face significant shortcomings in warehouse management, leading to increased costs and declining service quality. How can this situation be improved to ensure efficient warehouse operations? This article explores the importance of warehouse management from multiple perspectives and provides practical solutions to help distributors optimize their warehouse processes, improve operational efficiency, and ultimately achieve higher profitability.
1. The Importance of Warehouse Layout Planning
Effective warehouse layout is the first step toward improving management efficiency. A rational floor plan should be carefully designed based on product brands, fast-moving items, and transportation pathways. Distributors should consider the following aspects:
- Product Classification and Layout: Fast-moving products should be placed near shipping areas to reduce picking time and improve outbound efficiency. Bulkier items should be positioned near main aisles for easier handling and access.
- Aisle Design: Transportation pathways are critical. Aisles should have appropriate widths to ensure smooth movement for forklifts and other handling equipment, preventing delays caused by congestion.
- Storage Equipment and Tools: Selecting appropriate storage solutions—such as racks, pallets, and automated systems—can maximize space utilization and improve access efficiency. Proper handling tools like forklifts and carts can accelerate movement and reduce labor costs.
Through thoughtful warehouse layout planning, distributors can significantly improve access efficiency, minimize labor waste, and ensure employee safety during operations.
2. Enhancing Warehouse Functionality
A warehouse should not be viewed as merely a storage space but as a multifunctional operational platform. To improve professionalism and functionality, distributors should consider implementing the following measures:
- Functional Zoning: The warehouse should be divided into specialized areas such as inspection zones, storage zones, and packaging zones to ensure each operates efficiently.
- Specialized Facilities: Depending on product characteristics, install temperature-controlled or humidity-controlled storage equipment to maintain product quality. For example, perishable goods require climate-controlled environments, while chemicals need secure storage solutions.
- Auxiliary Service Areas: Establish dedicated office spaces, employee break rooms, and parking areas near the warehouse to reduce clutter and improve overall efficiency. This separation maintains cleanliness and ensures a better working environment.
3. Defining Management Responsibilities
Warehouse management roles should be clearly defined, including:
- Reviewing Inbound/Outbound Documents: Managers must carefully verify all shipping and receiving documents to maintain accurate inventory records.
- Quality Control and Feedback: Oversee product quantity and quality, promptly identifying and resolving issues while keeping upper management informed.
- Financial Coordination: Ensure all documents are forwarded to the finance department for clear accounting. Monthly reconciliation should be conducted to verify inventory and financial data consistency.
Clear role definitions help establish accountability, enabling efficient inventory management and timely problem resolution.
4. The Necessity of Safety Management
Warehouse safety cannot be overlooked. Comprehensive safety measures are essential to protect both employees and goods:
- Safety Protocols: Implement robust warehouse safety policies and ensure all employees receive proper training to recognize risks and take preventive actions.
- Theft and Fire Prevention: Install surveillance and alarm systems to enhance security. Firefighting equipment should be regularly inspected, and flammable materials should be stored separately.
- Proper Lighting and Equipment Safety: Adequate lighting ensures safe movement, while all handling equipment must meet safety standards to prevent accidents.
Effective safety management protects company assets and boosts employee morale.
5. Real-Time Inventory Control
Warehouses must support frontline sales with accurate, up-to-date inventory data. Sales teams unaware of stock levels risk shortages or overstocking. Implementing a "daily inventory reporting system" helps distributors stay informed through:
- Warehouse Management Systems (WMS): Advanced WMS solutions enable real-time monitoring and data analysis for quick decision-making.
- Regular Audits: Periodic stock checks ensure record accuracy, with discrepancies investigated promptly to prevent obsolescence.
- Sales-Warehouse Communication: Maintain strong coordination between sales and warehouse teams through shared platforms to adapt quickly to market changes.
6. First-In-First-Out (FIFO) Principle
Adhering to FIFO minimizes excess inventory and prevents product obsolescence:
- Labeling and Organization: Products should be labeled by arrival date and stored in designated zones for easy access.
- Sales Flow Monitoring: Adjust storage based on demand trends, allocating more space to high-turnover items.
- Regular Reviews: Continuous evaluation of stock movement helps identify slow-moving items for corrective action.
7. Dynamic Inventory Strategy Adjustments
Inventory management must evolve with market demands:
- Monthly Audits: Compare physical stock with sales data to assess inventory health.
- Market Analysis: Track consumer trends to optimize safety stock and purchasing volumes.
- Data-Driven KPIs: Use historical trends to set performance metrics like turnover rates for better oversight.
8. Managing Slow-Moving Inventory
Ineffective handling of stagnant stock leads to significant losses. Strategies include:
- Discount Promotions: Offer markdowns on quality goods with damaged packaging.
- Bundling: Pair slow sellers with popular items to boost sales.
- Disposal/Donation: Destroy defective items appropriately or donate usable products to enhance corporate responsibility.
Conclusion
Effective warehouse management reduces costs and maximizes profitability. In today's competitive market, mastering these strategies is essential. From layout optimization to safety protocols, real-time tracking to FIFO compliance—each element impacts performance. By continuously refining these processes, distributors can achieve operational excellence and sustain market leadership.