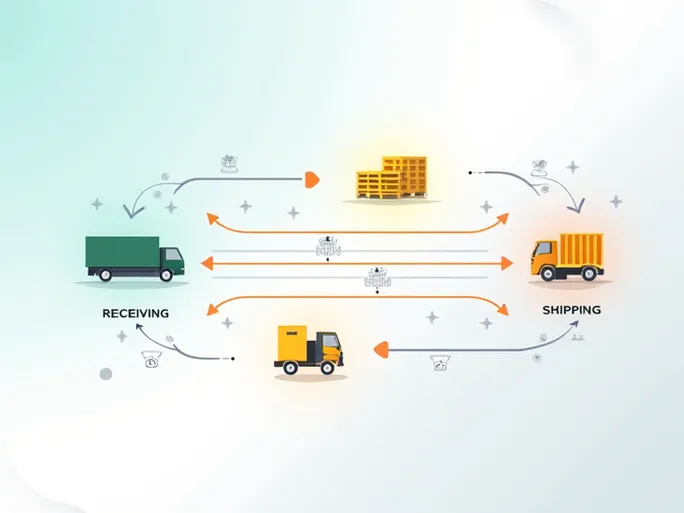
In today's increasingly complex and competitive market environment, warehouse management serves as a critical component of supply chain operations, directly impacting distributors' operational efficiency and profitability. Effective warehouse management can not only shorten logistics cycles but also enhance inventory turnover rates while reducing operational costs. However, many distributors face significant challenges in this area.
Current Challenges in Warehouse Management
1. Poor Warehouse Location and Design
Warehouse location and design significantly impact operational efficiency. Many distributors focus solely on storage capacity and security when selecting facilities, overlooking actual operational needs. Repurposed factories or older warehouses may temporarily solve storage problems, but their poor space planning and insufficient pathways often create logistical bottlenecks that slow down the entire supply chain. In high-volume operations, overcrowded spaces increase the risk of product damage.
2. Disorganized Product Placement
Many warehouses follow an ad-hoc "nearest available space" approach to product placement, lacking systematic classification and standardized management. While this may seem convenient short-term, it leads to severely inefficient space utilization as product variety and volume grow. This disorganization wastes employee time in locating items and often results in obsolete inventory accumulation and internal theft. Misplaced items further compound operational inefficiencies.
3. Mixed-Use Facility Issues
Some distributors combine warehouses with other functions like employee housing or vehicle storage, creating environmental chaos that limits professional operations and poses safety risks. These mixed-use environments make inventory management more difficult and significantly reduce operational efficiency.
4. Unclear Warehouse Staff Roles
Warehouse personnel responsibilities are often oversimplified to "guarding the warehouse" without clear task assignments. This lack of definition prevents staff from properly monitoring inventory fluctuations or maintaining proper environmental conditions (temperature, humidity), potentially compromising product quality and wasting resources.
5. Obsolete and Near-Expiration Products
Poorly managed warehouses frequently accumulate obsolete and soon-to-expire products that occupy valuable space, disrupt supply chain operations, and create financial pressures. In extreme cases, expired goods can cause cash flow problems that impact daily operations.
Lean Management Solutions
Distributors must recognize that warehouse performance directly affects overall supply chain efficiency. Lean management principles—focusing on maximizing value while minimizing waste—offer effective improvement strategies:
1. Strategic Location and Layout Planning
Warehouse selection should consider multiple factors including transportation access, goods flow requirements, and customer needs. As businesses grow, investing in specialized or company-owned facilities becomes essential. Layout design must prioritize efficiency through proper aisle widths, loading areas, and clearly labeled storage sections.
2. Dedicated Warehouse Spaces
Maintain warehouse environments exclusively for inventory management by separating them from living quarters and other functions. Establish clear operational procedures and standards to enhance professional management.
3. Defined Staff Responsibilities
Clearly outline warehouse personnel duties including receiving, shipping, inventory control, and exception handling. Regular training ensures staff understand modern warehousing concepts and can effectively monitor operations.
4. Regular Audits and FIFO Implementation
Conduct periodic inventory checks to identify damaged or expired products. Organize storage by product characteristics and enforce First-In-First-Out (FIFO) principles—especially for perishables—to minimize obsolete inventory.
5. Inspection and Monitoring Systems
Implement surprise audits and establish performance metrics to maintain staff accountability. Documentation through logs and reports helps identify issues and adjust strategies promptly.
6. Technology Integration
Warehouse Management Systems (WMS) enable real-time inventory tracking and automate processes like receiving, shipping, and transfers while reducing human error. Data analytics can predict demand fluctuations and optimize inventory strategies.
7. Organizational Optimization
Effective warehouse management requires cross-functional teams including operations managers, warehouse staff, and logistics coordinators. Collaboration improves efficiency and fosters knowledge sharing, creating a stronger operational culture.
Conclusion
Implementing lean management principles in warehouse operations enhances professionalism while improving supply chain efficiency and reducing costs. Through continuous optimization, distributors can strengthen their market position. Each incremental improvement creates competitive advantages, enabling faster response to market changes and increased market share. In an uncertain business environment, proactive lean transformation of warehouse management will be crucial for long-term success.