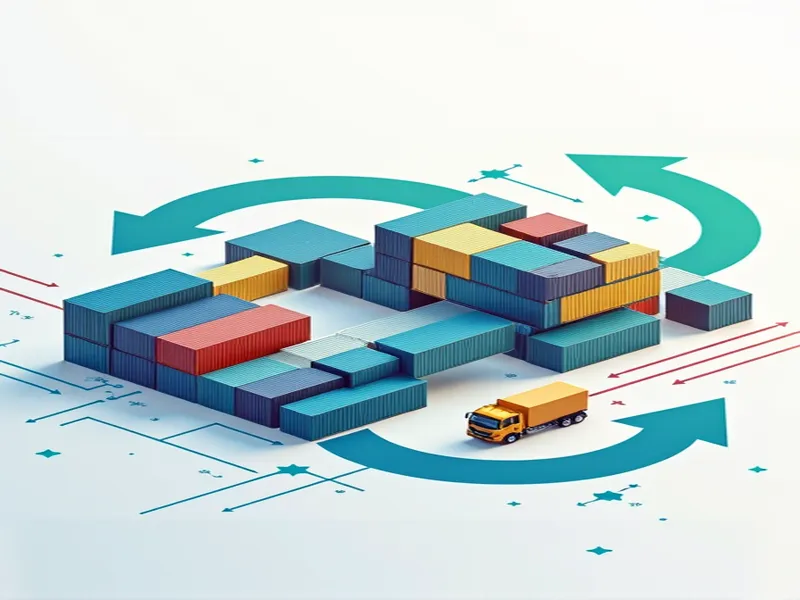
In today's complex international logistics environment, warehouse overflow issues have become increasingly common, presenting significant challenges for logistics companies, particularly those in maritime shipping. Recently, a well-known fleet notified its customers that container release was impossible due to warehouse overflow, leaving many clients confused about potential solutions and inquiring whether additional fees could resolve the situation. The fleet responded that negotiations with agents and shipping companies would be necessary to find appropriate solutions.
First, it's essential to understand that warehouse overflow typically results from limited shipping company capacity. In such scenarios, the primary risk for customers is cargo rollover—particularly problematic in an era where shipping timelines have become critically important. Any delays can lead to customer dissatisfaction. Notably, container release restrictions aren't solely caused by overall shipping conditions; they may also stem from complex port area pickup and release arrangements that warrant deeper examination.
Container release restrictions generally occur for two reasons: either the yard has no available containers, or the shipping company has stopped releasing containers. In the first scenario, when containers are unavailable at the yard, possible solutions include paying additional fees or contacting the shipping company to request relocation to another yard. This flexible approach often resolves immediate difficulties in practical operations.
The second scenario proves more complicated. When shipping companies halt container releases, customers typically have no choice but to wait. Decision-making authority shifts entirely to the shipping company as they manage subsequent cargo arrangements, leaving customers with few intervention options.
Without proper contingency plans, warehouse overflow can directly prevent container retrieval, creating significant anxiety for customers. While financial resources might occasionally secure alternative solutions—such as quickly transferring to available containers—this approach carries risks. Obtaining containers without proper arrangements may lead to failure in timely loading, potentially resulting in additional storage and container rental fees that compound the problem. Therefore, from a management perspective, handling warehouse overflow requires careful consideration of actual conditions, maintaining open communication with sales teams, and developing optimal solutions.
Equipment order issues triggered by warehouse overflow also demand attention. When companies receive equipment orders, they should immediately verify yard inventory status to prevent oversight that could lead to more complex problems. While warehouse overflow presents challenges, proactive communication with relevant personnel to understand actual yard inventory—combined with rational decision-making based on operational capacity—can effectively minimize losses and establish a stronger foundation for future operations.
Conclusion: Managing warehouse overflow is no simple task. Companies must approach it multilaterally, maintaining close contact with shipping companies and agents while considering all factors that might affect cargo retrieval. Timely communication and flexible response measures can mitigate some losses caused by overflow. In today's increasingly competitive market environment, adaptable responses to unexpected situations help companies build stronger foundations for future success.