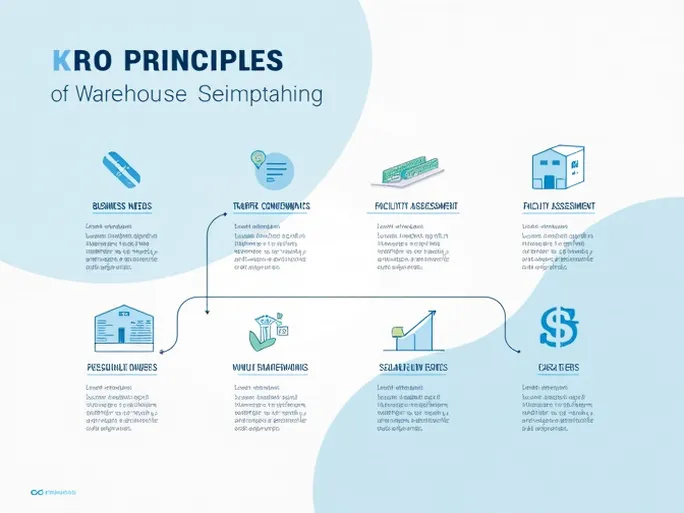
In today's competitive economic landscape, warehouse selection has evolved from a simple logistical decision to a critical factor determining business success. Despite operating in increasingly fierce markets, many companies still rely on experience-based warehouse choices, often neglecting long-term strategic planning. This article examines how to approach warehouse selection systematically to ensure operational efficiency and business continuity.
Core Principles of Warehouse Selection
1. Defining Business Requirements
The foundation of effective warehouse selection begins with clearly understanding your operational needs. Key considerations include:
- Product variety and inventory volume
- Shipping frequency requirements
- Seasonal demand fluctuations
Thorough analysis of these factors helps determine the optimal warehouse type, size, and storage specifications.
2. Transportation Accessibility
Location significantly impacts supply chain efficiency. Ideal warehouse sites should:
- Proximity to major transportation hubs (highways, airports)
- Minimal traffic congestion
- Appropriate vehicle access dimensions
- For e-commerce: accessibility for workforce recruitment and logistics partners
3. Facility Infrastructure
Comprehensive facility assessments should verify:
- Availability of essential equipment (racking, forklifts, scales)
- Security and fire prevention systems
- Overall condition and maintenance standards
4. Operational Management Quality
Evaluate the warehouse management team's competence through:
- Documented standard operating procedures (SOPs)
- Process implementation effectiveness
- Staff training and performance metrics
5. Scalability Potential
Forward-thinking businesses must consider:
- Available expansion space for future growth
- Flexibility for functional modifications
- Adaptability to evolving business needs
6. Cost Analysis
Comprehensive cost evaluation should include:
- Direct costs (rent, utilities, handling fees)
- Indirect costs (transportation, time efficiency)
- Long-term value versus short-term savings
Key Selection Criteria
1. Space Configuration
Optimal warehouse layouts feature:
- Square or near-square dimensions for operational efficiency
- Adequate space for current and projected workflow
- Potential for future reconfiguration
2. Vertical Clearance
Height considerations should account for:
- Maximum vertical storage capacity
- Future storage system upgrades
- Specialized equipment requirements
3. Warehouse Typology
Selection should align with:
- Product characteristics (temperature sensitivity, hazard classification)
- Industry-specific requirements
- Potential for multi-functional use
4. Physical Infrastructure
Essential structural elements include:
- Building integrity and loading areas
- Dock configurations and access points
- Internal material handling systems
Conclusion
Strategic warehouse selection forms the foundation for both immediate operational success and long-term business growth. By methodically evaluating business requirements, location advantages, facility quality, management capabilities, scalability, and cost factors, companies can make informed decisions that enhance supply chain performance. In today's competitive environment, optimized warehouse operations provide significant competitive advantages, enabling businesses to achieve greater efficiency and position themselves for future success in an increasingly digital logistics landscape.