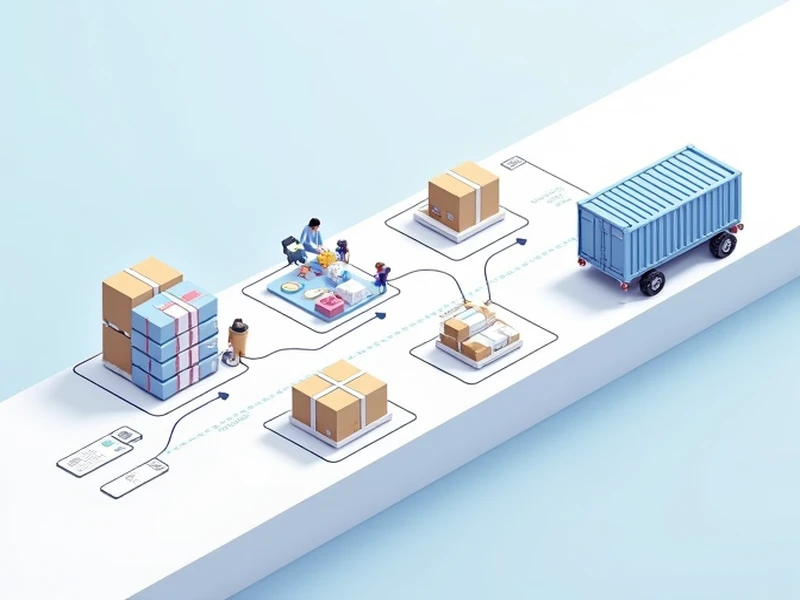
In the logistics industry, Less-than-Container Load (LCL) shipments must adhere to strict warehousing and loading protocols during transportation. The following procedures ensure safe and compliant cargo handling:
Pre-Loading Preparation: Damaged packaging must be repaired or replaced to meet container transportation standards. Shipping marks require verification and reprinting when necessary, with confirmation from cargo owners. Goods from multiple shippers should be systematically arranged in designated areas prior to container loading.
Container Specification Verification: Logistics personnel must confirm appropriate container types (20', 40', or 40' high cube) based on cargo volume and characteristics.
Cargo Protection Measures: Implement separation boards between shipments to prevent packaging damage and mark smearing. Apply anti-contamination and moisture-proof treatments as needed. Conduct accurate packaging strength assessments to determine optimal stacking heights.
Weight Distribution Principles: Heavy items must be placed at container bottoms with lighter goods positioned above. Maintain balanced weight distribution throughout the container to prevent structural deformation during handling and maritime transport.
Documentation Requirements: Container receipt forms must include detailed information such as:
- Total piece count
- Delivery date
- Vessel name
- Bill of lading number
- Damage reports (if applicable)
Loading Best Practices: Ensure cargo arrangement minimizes empty spaces to prevent shifting during transit. When using wooden supports or dunnage, verify materials are clean, dry, and contamination-free.
Post-Loading Verification: Cross-check loaded cargo against shipping manifests for:
- Piece count accuracy
- B/L number correspondence
- Marking consistency
Information Reporting: Operations teams must promptly communicate loading details and inventory status to company shipping routes, maintaining precise logistical coordination throughout the transportation chain.