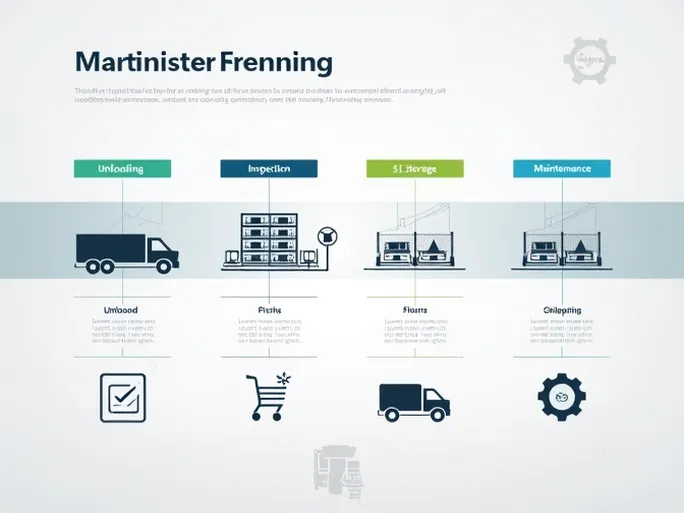
In today's rapidly evolving economic landscape, businesses face increasingly intense competition, particularly in logistics and supply chain management. Warehouse optimization has become crucial—these facilities are no longer just storage spaces but critical nodes in business operations and customer service. Streamlining warehouse processes can significantly boost efficiency, reduce operational costs, and ultimately enhance market competitiveness. But what exactly constitutes warehouse operations, and how can businesses achieve peak efficiency in these complex workflows?
I. Core Components of Warehouse Operations
Warehouse workflows typically encompass multiple stages of goods handling, including unloading, inspection, storage organization, inventory maintenance, picking, loading, and shipment. While each represents a distinct process, these elements are deeply interconnected. The key components include:
- Unloading: The initial stage when goods arrive requires skilled personnel to handle items without damage, setting the tone for subsequent processes.
- Inspection: Quality and quantity verification ensures received goods match purchase orders, with barcode technology increasingly enhancing accuracy.
- Storage Organization: Proper classification and space optimization minimize handling time and maximize storage density.
- Inventory Maintenance: The heart of warehouse operations, preserving product quality throughout the storage period.
- Order Picking: Directly impacts customer satisfaction through efficient fulfillment strategies and workforce management.
- Loading & Shipping: The final link in the chain requires precision to minimize delivery delays.
II. The Imperative of Seamless Workflow Integration
Smooth transitions between warehouse stages dramatically improve efficiency while reducing resource waste. Operational bottlenecks in any single area can cascade through the entire system, making regular process evaluations essential for continuous improvement.
1. Efficiency Enhancement Strategies
Modern warehouses employ data analytics and system integration to optimize workflows. For instance, implementing ABC classification—positioning high-velocity items closer to shipping areas—can significantly reduce picking times.
2. Adaptive Operations Management
Seasonal fluctuations and market shifts demand dynamic operational adjustments. Predictive analytics enable real-time inventory monitoring and proactive replenishment strategies.
III. Technological Advancements in Warehouse Optimization
The digital transformation of warehouse management has introduced powerful tools for operational enhancement:
- Automation: Robotic systems like automated storage/retrieval machines (AS/RS) and autonomous mobile robots reduce human intervention while improving safety.
- Warehouse Management Systems (WMS): Centralized platforms providing real-time inventory visibility and decision-support analytics.
- Auto-Identification: Barcode and RFID technologies enable precise inventory tracking and status updates.
- Predictive Analytics: AI-driven demand forecasting and automated replenishment systems create agile, intelligent operations.
IV. Theoretical Framework for Process Optimization
Effective warehouse optimization requires customized theoretical analysis across several dimensions:
- Temporal Efficiency: Minimizing idle time between operational stages through precise scheduling.
- Spatial Optimization: Strategic product placement reduces travel distances, particularly when high-turnover items occupy prime locations.
- Process Streamlining: Eliminating redundant steps through workflow analysis and adopting assembly-line concepts.
- Organizational Alignment: Coordinating human and equipment resources across all operational phases.
- Workforce Development: Investing in employee training and optimal staffing configurations to reduce errors.
V. Case Study: E-Commerce Warehouse Transformation
A prominent global e-commerce company demonstrated the transformative power of warehouse optimization through intelligent systems implementation. Their solution featured:
- Real-time inventory monitoring via mobile scanning devices
- AI-powered picking systems that intelligently allocate tasks
- Big data analytics for sales trend prediction and inventory control
This approach yielded dramatic improvements in fulfillment speed and inventory turnover, providing a replicable model for industry peers.
VI. Future Outlook and Conclusion
Warehouse optimization represents a holistic transformation rather than incremental improvements. The future points toward intelligent, data-driven operations where:
- Digital technologies will increasingly automate decision-making
- Real-time analytics will enable unprecedented operational agility
- Cross-functional collaboration will become essential for peak performance
By embracing these innovations, businesses can transform their warehouses from cost centers into strategic assets that drive competitive advantage in an increasingly demanding marketplace.