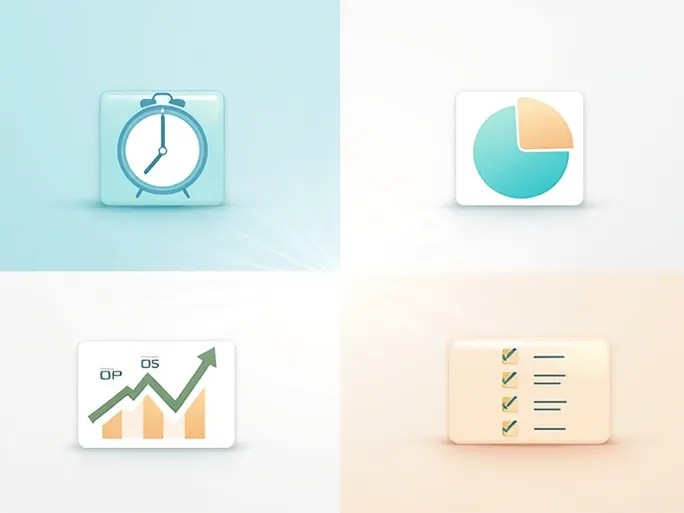
In modern business operations, the importance of inventory management has become increasingly evident. Finding the right balance between safety stock and cost is crucial for business success. While excessive inventory may demonstrate a company's strength, it also leads to increased storage costs and capital tie-up issues. Conversely, zero inventory might reduce costs but could negatively impact production efficiency and customer satisfaction. Proper inventory management not only enhances a company's financial performance but also improves customer satisfaction and market competitiveness. This article explores four mature and effective inventory management methods to help businesses address inventory challenges, optimize operational capabilities, and improve overall efficiency.
1. Just-in-Time (JIT) Inventory Management
Just-in-Time (JIT) is an advanced production philosophy designed to improve efficiency and reduce inventory through highly synchronized production processes and demand-aligned material management. Its core principle revolves around "the right time, right quantity, and right items." Suppliers provide exactly what's needed based on the buyer's specific requirements, ensuring smooth production flow.
Basic Concepts and Principles of JIT
In traditional production models, large inventories serve as safety buffers against uncertain market demands or production disruptions. However, this approach often leads to excessive capital tie-up, rising storage costs, and product obsolescence risks. JIT implementation aims to fundamentally change this situation by encouraging businesses to closely align production processes with market demands through refined demand forecasting, production planning, and material procurement.
Kanban Management in JIT
In JIT production systems, kanban management serves as a critical tool. Originating from Toyota, kanban uses visual signals (such as cards, light boards, or electronic panels) to communicate production and material requirements. By synchronizing production instructions with actual demand, it prevents overproduction and inventory buildup.
Kanban management operates in two primary forms: production kanban and replenishment kanban. Production kanban indicates how many products the production line needs, prompting immediate production in preceding processes. Replenishment kanban signals material requirements, allowing preceding processes to supply components only when subsequent processes explicitly demand them. Kanban not only improves information flow efficiency but also significantly reduces unnecessary inventory and associated costs. Additionally, kanban systems enable real-time production monitoring for quick response to changing customer demands.
Challenges in JIT Implementation
Despite its advantages, JIT presents implementation challenges. First, it demands extremely high supply chain reliability. Successful JIT requires suppliers to provide consistently dependable and fast service—any delivery failure could halt production lines. Second, internal collaboration and communication must improve to ensure seamless coordination across all operational stages. Employee training also proves essential, as only properly trained staff who understand and execute JIT processes can deliver its full benefits. Therefore, businesses must develop comprehensive strategic plans and conduct feasibility assessments before JIT implementation.
2. ABC Analysis Method
The ABC Analysis Method categorizes inventory into A, B, and C classes based on importance, enabling differentiated management. By focusing resources on Class A items, businesses can improve capital efficiency while controlling costs and enhancing output value.
Implementation of ABC Classification
Class A Inventory: High value, low quantity. Typically representing 70-80% of total inventory value but only 10-15% of total items, these goods require strict management including regular inspections, accurate demand forecasting, and minimized stockpiling to prevent production disruptions.
Class B Inventory: Moderate value and quantity. Accounting for 15-25% of total inventory value, these items need periodic review and analysis with moderate control to maintain appropriate stock levels.
Class C Inventory: Low value, high quantity. Management can be more relaxed, using simplified methods like larger orders with reduced frequency. Despite low unit value, their aggregate impact on inventory can be substantial.
Resource Allocation and Management Optimization
ABC classification enables appropriate resource allocation. For Class A items, businesses might set higher safety stock levels to accommodate demand fluctuations, while Class C items could use economic order quantities to reduce carrying costs and ordering frequency. This rational resource distribution effectively optimizes inventory management, improves capital turnover, and reduces operational risks.
3. Economic Order Quantity (EOQ)
The Economic Order Quantity method optimizes order quantities to minimize total storage and ordering costs. This model identifies an ideal order quantity that balances ordering and carrying costs.
Basic Assumptions of the EOQ Model
EOQ analysis requires: 1) constant inventory consumption during the analysis period; 2) fixed ordering and carrying costs; and 3) timely inventory replenishment. Best suited for stable demand environments, it helps businesses make informed inventory decisions.
EOQ Calculation and Implementation
The EOQ formula is:
EOQ = √(2DS/H)
Where D represents annual demand, S is the fixed cost per order, and H is the annual holding cost per unit. Calculating EOQ helps determine optimal order quantities for cost reduction.
In practice, EOQ effectiveness depends on accurate demand data analysis. For volatile demand, businesses might combine EOQ with other methods like safety stock to increase flexibility. Given its assumption of uniform demand, EOQ has limited application scenarios, making integrated approaches with other inventory tools more effective.
4. Reorder Point Method
The Reorder Point Method establishes replenishment triggers when inventory falls to predetermined levels. This ensures continuous production by preventing stockouts.
Reorder Point Calculation and Application
The reorder point formula is:
R = d × L + B
Where R is the reorder point, d represents average daily demand, L is lead time, and B is safety stock. This enables real-time inventory monitoring and timely replenishment decisions.
Accurate lead time management proves critical. Businesses should consider supply chain uncertainties—including supplier delivery capabilities and raw material market fluctuations—to ensure reorder points adapt to dynamic market conditions. Regular evaluation and adjustment based on historical data and market trends enhances responsiveness and adaptability.
Conclusion
Inventory management forms a foundation for business success. Effective inventory control not only reduces operational costs but also enhances customer satisfaction and ensures stable production capacity. By properly implementing these four methods—JIT, ABC Analysis, EOQ, and Reorder Point—businesses can optimize inventory operations while strengthening flexibility in dynamic markets.
When developing inventory strategies, companies must consider their size, industry characteristics, and market environment to select appropriate tools. Strengthening supply chain coordination and integrating information systems will improve overall inventory management efficiency. The right inventory strategy helps businesses gain competitive advantages and achieve sustainable growth. Through continuous adjustment and optimization, companies can maintain competitiveness in rapidly changing business environments while pursuing long-term development goals.