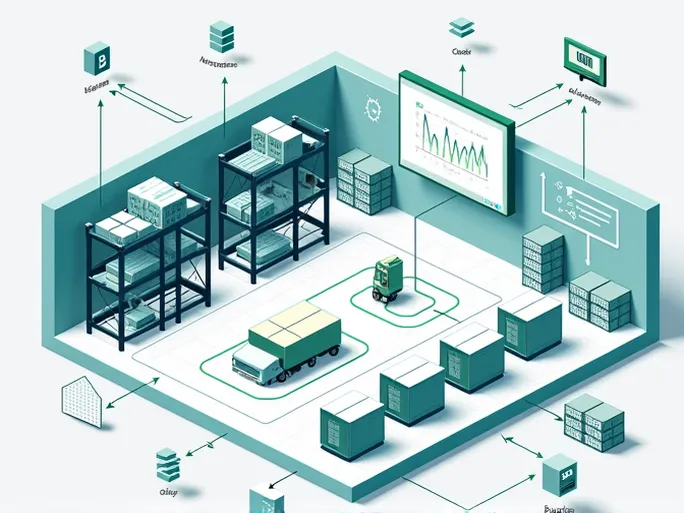
In today's business environment, logistics management has become a vital component across all industries. Within this complex supply chain, warehouse labeling and storage location management play particularly crucial roles. These systems not only impact storage efficiency but also significantly influence operational costs and customer satisfaction. Optimizing warehouse labeling and storage management has become an essential pathway for businesses to enhance their competitiveness.
I. The Importance of Label Management
In our information-driven society, warehouse management has evolved beyond simple item storage to encompass comprehensive processes from item receipt and storage to final delivery. Label management serves as the foundation of these operations, acting as the central nervous system of warehouse activities. Through scientific and rational labeling, businesses can achieve precise tracking of every item, significantly improving warehouse operational efficiency.
- Enhanced Operational Efficiency: Modern warehouses increasingly utilize automation and digital technologies. Clear labeling systems enable faster item picking and transportation, reducing search times and improving overall productivity.
- Error Reduction: Clear labeling effectively minimizes mistakes and confusion. Standardized labels allow warehouse staff to easily identify storage locations, reducing losses from operational errors and making management more efficient.
- Improved Customer Satisfaction: Effective logistics management enhances customer satisfaction. In e-commerce, for example, order accuracy and timely delivery directly impact customer experience. Efficient warehouse labeling and management help businesses better meet customer needs and strengthen loyalty.
II. Principles of Label and Storage Location Management
To achieve efficient warehouse management, several key principles should be followed:
1. Clarity and Standardization
- Uniqueness: Each item should have a unique identifier, enabling staff to quickly locate products during storage, inventory checks, or shipping.
- Standardization: Label formats should be uniform and standardized, enhancing corporate image while facilitating quicker onboarding for new employees.
2. Process Differentiation
Reasonable zoning within warehouses facilitates item management and reduces staff workload. For example, categorizing products by type or purpose prevents time wasted searching for items.
3. Environmental Requirements
Selecting appropriate storage environments is crucial. Temperature- or humidity-sensitive items require specially designed conditions to maintain integrity, extend shelf life, and build customer trust in product quality.
III. Storage Location and Inspection Area Design
Scientifically designed storage locations and inspection areas can dramatically improve operational efficiency.
1. Buffer Zones
Buffer zones act as warehouse "shock absorbers," regulating item flow during peak receiving or shipping periods to prevent bottlenecks. Design should consider width and depth for optimal staff and equipment operation.
2. Inspection Areas
Items require quality inspection upon arrival. Inspection areas should maintain independence and privacy to avoid disrupting normal warehouse operations.
IV. Label Characteristics and Management Functions
Effective label management incorporates several key features:
- Coding Principles: Use memorable alphanumeric codes (e.g., "A1," "B1") for quick staff recognition.
- Management Advantages: Efficient labeling reduces costs while improving inventory accuracy and enabling data-driven stock management for better purchasing decisions.
V. Implementation Methods
Establishing a scientific labeling and storage management system requires several steps:
- Zone Division: Clearly define each warehouse area's function for orderly operations.
- Sub-Numbering: Implement secondary numbering (e.g., A1, A2) for detailed management.
- High-Rack Labeling: Use granular numbering (e.g., A01-01) for intuitive high-shelf item retrieval.
- Aisle Design: Create appropriately wide aisles considering usage frequency and material handling needs.
VI. Functional Area Classification
Scientific zoning of warehouse functions significantly improves management efficiency. Key areas include:
- Service Counters: Primary areas for customer service and information.
- Storage Zones: Categorized product storage for efficient retrieval.
- Operations Areas: Designed workspaces to streamline inbound/outbound processes.
Such zoning combined with alphanumeric coding enhances organization while dramatically reducing item search times.
Conclusion
Warehouse labeling and storage management represent indispensable components of modern logistics. Scientific labeling systems enable more efficient, accurate operations that boost productivity while enhancing customer satisfaction and competitive advantage. Prioritizing systematic, standardized warehouse management helps businesses navigate intense market competition successfully. For further insights into warehouse operations best practices, we welcome your inquiries about achieving logistics excellence.