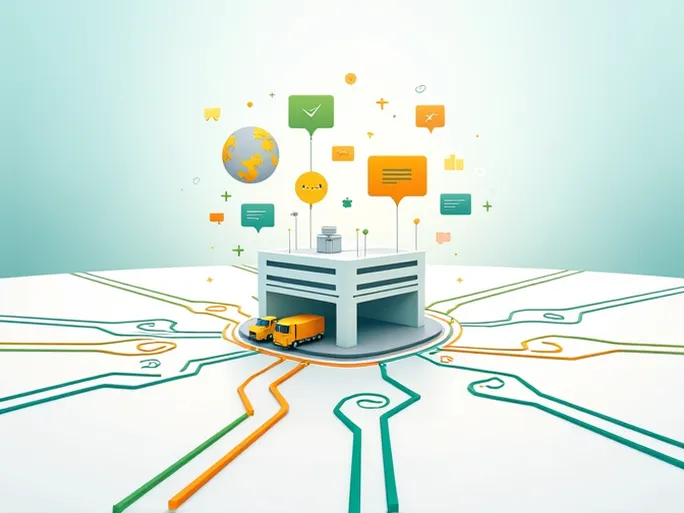
In contemporary corporate supply chains, warehouse departments serve as far more than mere storage facilities—they function as critical operational hubs and vital collaboration bridges between business units. While many perceive warehouse operations as simply revolving around inventory management, their actual responsibilities extend much further throughout the organization.
Consider the consequences when procurement departments make purchasing decisions without consulting warehouse capacity limitations. Warehouse managers inevitably face overwhelming inventory surges that exceed storage capabilities, potentially triggering exponential cost increases. In such scenarios, warehouse teams bear the brunt of other departments' decisions—an unfair dynamic that demands systemic solutions.
When inventory backlogs or impending expirations occur, warehouse departments frequently become the default scapegoats. To transform this counterproductive pattern, warehouse managers must prioritize relationship-building across the organization. Effective communication with both sales and procurement teams proves essential for preventing responsibility confusion and resource mismanagement. This collaborative approach transcends warehouse operations—it enhances overall organizational efficiency when implemented company-wide.
Timely information sharing represents another critical success factor in today's digital landscape. Warehouse managers should proactively communicate inventory status updates and impending expiration alerts to relevant stakeholders. Early warnings and cross-departmental coordination can significantly mitigate operational burdens. When information flows transparently throughout an organization, overall efficiency improves dramatically.
Superior enterprises consistently prioritize communication skills during talent acquisition, recognizing their fundamental importance to operational success. In warehouse management specifically, inadequate communication channels frequently trigger cascading failures that compromise organizational performance. For instance, when inventory shortages go unreported to sales teams, consequences extend beyond stockouts to potential customer attrition and reputational damage.
Breaking down departmental silos requires proactive bridge-building from warehouse leadership. Managers should establish dedicated communication platforms that encourage team members to seek support rather than struggle independently. This cultural shift prevents the destructive cycle of poor communication leading to compounding problems. Regular cross-functional meetings offer particularly effective forums for aligning warehouse capabilities with sales forecasts and procurement plans.
Beyond interdepartmental coordination, warehouse leaders must cultivate open dialogue within their teams. Understanding staff challenges, constraints, and suggestions enables optimized workflows and morale enhancement. Successful managers balance strategic planning with active listening—conducting regular one-on-one sessions to identify and resolve operational pain points. Creating open feedback channels makes employees feel valued while strengthening team cohesion.
For managers seeking concrete communication improvements, structured training programs deliver measurable results. Continuous skill development ensures teams remain effective amid evolving operational demands. Technological solutions like barcode tracking systems exemplify how tool adoption can streamline processes when combined with strong team communication—ultimately boosting organizational performance.
The digital transformation wave presents both challenges and opportunities for warehouse operations. As manual processes give way to smart warehousing solutions, managers must identify necessary skill upgrades and technological implementations. Data analytics tools now enable real-time inventory monitoring and predictive demand forecasting—capabilities that reduce waste while optimizing resource allocation.
Process standardization represents another critical improvement area. Implementing clear warehouse management protocols with well-defined responsibilities prevents confusion and resource misuse. Regular performance reviews and incentive programs can further enhance operational quality while encouraging continuous improvement.
Modern warehouse managers bear significant responsibility for organizational efficiency. By fostering open communication, addressing staff concerns, and promoting cross-functional collaboration, they can maintain high-performing teams despite operational pressures. Strategic adoption of supply chain software and analytical tools adds scientific precision to warehouse management.
In today's competitive landscape, warehouse operations have evolved from simple storage functions to strategic supply chain differentiators. Managerial excellence now requires equal mastery of technical systems and leadership principles—plus the adaptability to leverage emerging technologies. Regardless of future challenges, warehouse leaders who maintain situational awareness and responsive decision-making will position their organizations for sustainable success.