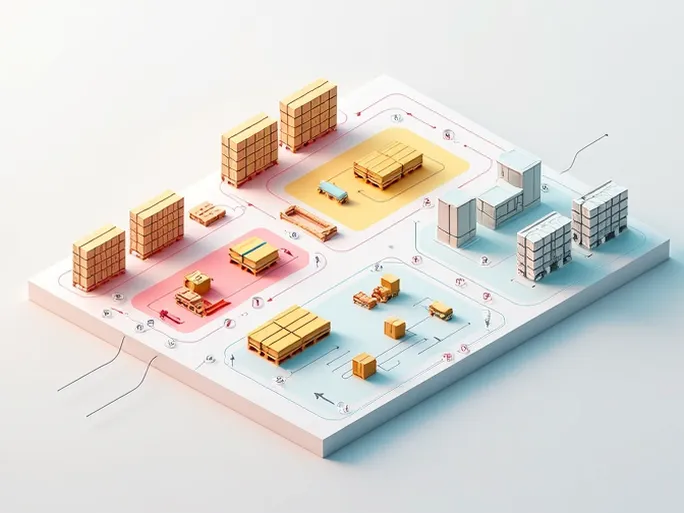
In today's highly competitive logistics industry, warehouse and distribution center operations face numerous challenges that demand immediate solutions. While companies often focus on building new facilities, acquiring advanced equipment, and expanding existing infrastructure to improve efficiency, they frequently overlook the crucial aspects of slotting optimization and daily management—oversights that can significantly impact overall operational performance.
Effective slotting strategies not only maximize limited storage space but also dramatically enhance operational efficiency, directly influencing both operational costs and customer service levels. This makes re-evaluating the core value and practical applications of slotting optimization in warehouse management particularly crucial.
I. The Core Value of Slotting Optimization
Slotting optimization can be defined as the strategic placement of inventory within a warehouse based on facility characteristics and product attributes to optimize material handling and improve space utilization. In traditional warehouse operations, approximately 60% of operational time is spent on worker movement—meaning proper slotting can significantly reduce non-value-added labor.
Considering that labor costs account for 40-50% of total warehouse operating expenses, minimizing travel distance becomes paramount. Imagine pickers in a poorly organized warehouse crisscrossing the facility for every SKU, wasting tremendous time and labor resources. Effective slotting is therefore essential for improving overall warehouse productivity.
For instance, placing high-velocity items near receiving areas can substantially accelerate inbound operations, while positioning frequently picked or replenished items close to shipping docks can dramatically reduce picker working time. Despite these obvious benefits, many warehouse managers fail to fully appreciate slotting's potential in daily operations. The absence of scientific slotting management ultimately leads to wasted human resources and diminished customer satisfaction.
In this context, warehouse managers must reassess the true significance of slotting optimization to maintain competitive advantage in today's demanding market.
II. Practical Applications of Slotting Optimization
Beyond improving operational efficiency, effective slotting management generates positive impacts across multiple dimensions. For example:
• Arranging standard items according to picking sequences can significantly reduce the number of pick positions required
• Properly adjusting replenishment and picking quantities can alleviate operator workload and shorten operational cycles
• Separating similar-looking items reduces picking errors and enhances service quality
Ergonomic principles should guide optimal placement decisions—heavier items positioned at waist level for easier handling, fragile goods placed in protected areas to minimize damage risk. Such layouts not only improve pallet and container loading efficiency but also prevent unnecessary reinvestment due to stockouts.
Through meticulous planning, warehouses achieve greater operational flexibility and scientific management, creating substantial economic benefits. Whether building new facilities or retrofitting existing ones, proper slotting represents a critical strategy for achieving operational excellence with minimal investment.
III. Implementing Slotting Optimization
Successful slotting implementation requires thorough preparation including strategy selection, goal setting, data collection, and requirements analysis.
Goal Setting: Establish both efficiency targets (reduced travel distance, lower replenishment frequency, improved picking accuracy) and account for constraints (item weight, slot dimensions, picking precision requirements). Prioritize objectives to guide subsequent planning.
Data Collection: Focus on gathering slot identity information and product demand data to understand inventory dynamics and develop targeted management strategies.
Requirements Analysis: Examine each SKU's picking and replenishment characteristics by analyzing shipment volumes and frequency. Classify inventory using ABC analysis—typically, fast-moving A-items (10-20% of SKUs) account for 70-90% of shipments. Select appropriate picking equipment (manual carts, powered systems) based on product characteristics and calculate optimal replenishment quantities to ensure operational flexibility.
IV. Slotting Strategy Execution
Post-analysis implementation involves two primary steps: zone designation for product categories followed by detailed slot planning. For complex logistics systems with multiple functional areas and diverse picking equipment, zoning significantly enhances overall efficiency by enabling clearer management and flexible resource allocation.
Ultimately, slotting optimization isn't merely a warehouse management component—it's a vital productivity driver. Companies must continuously evaluate their slotting strategies as a competitive differentiator. Scientific, rational slotting planning positions organizations for market leadership through enhanced customer satisfaction and market share.
As the logistics industry evolves, scientifically grounded slotting strategies will empower companies to maintain operational excellence amid market volatility while driving sustainable growth.