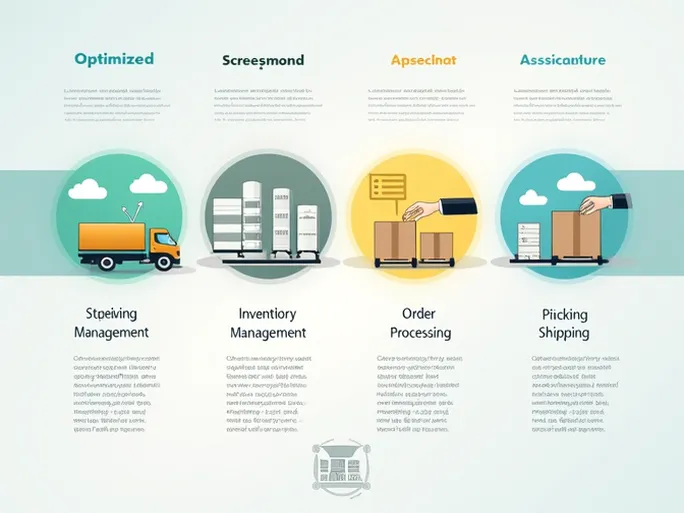
In today's competitive supply chain environment, optimizing internal warehouse processes to ensure efficient logistics operations has become a core challenge for businesses. With the rapid development of the global economy and increasingly diverse and personalized customer demands, companies face higher efficiency requirements and cost pressures. Warehouse operations encompass all processes from goods receipt to shipment, directly impacting corporate costs, service levels, and market responsiveness. Therefore, optimizing the effectiveness and efficiency of warehouse processes is particularly crucial. This article will explore key aspects of warehouse management to provide guidance for achieving operational excellence.
I. The Foundation of Warehouse Operations
Warehouse operations form the basis of internal logistics activities. These processes not only facilitate material flow but also reflect operational efficiency, typically consisting of several key components: goods receipt, storage, inventory management, order processing, order picking, packaging, and shipment. The efficient operation of each component can reduce operational costs while improving customer satisfaction, thereby enhancing market competitiveness.
1. Goods Receipt
As the starting point of warehouse operations, efficient goods receipt is crucial for overall logistics performance. An effective receiving process should include these standard procedures: advance notification, arrival confirmation, quality inspection, quantity verification, information entry, and goods storage.
Before goods arrive at the warehouse, advance notification should be provided to facilitate preparation. Upon arrival, transportation documents should be verified against the actual goods. Quality inspections should then ensure compliance with standards. After quantity confirmation, information should be promptly entered into the system for inventory tracking. Finally, qualified goods should be stored efficiently.
To improve receiving efficiency, companies should implement integrated information systems including Electronic Data Interchange (EDI), Transportation Management Systems (TMS), and Warehouse Management Systems (WMS) to ensure real-time information flow and minimize delays and errors. Digital analysis of receiving data can help identify potential issues for timely adjustments.
2. Storage Management
Effective storage management is fundamental to warehouse operations, involving optimal space utilization. Storage should follow these principles: product classification, FIFO (First-In-First-Out) implementation, space optimization, safety, and accessibility.
Products should be categorized based on characteristics, sales frequency, and storage requirements to facilitate access and prevent damage or expiration. FIFO principles reduce risks of obsolescence. Space optimization through proper layout design maximizes storage capacity.
Regular warehouse layout evaluations should be conducted. Modern WMS solutions enable real-time tracking of goods movement, optimize placement, and generate data reports for management decisions.
3. Inventory Management
Effective inventory management prevents overstocking or shortages, saving costs while improving responsiveness. Key strategies include ABC classification, Economic Order Quantity (EOQ) models, and safety stock policies.
ABC classification prioritizes inventory by value: A-items (high value, low quantity) require tight control; B-items (moderate value/quantity) use periodic reviews; C-items (low value, high quantity) employ relaxed management. This approach balances cost savings with operational continuity.
EOQ models calculate optimal order quantities to minimize holding and ordering costs. Safety stock policies buffer against demand fluctuations. Combined, these strategies enhance inventory accuracy and business performance.
4. Order Processing
Order processing connects customers with businesses, directly impacting satisfaction and revenue. The process typically includes order receipt, confirmation, inventory verification, fulfillment preparation, and shipping arrangements.
Modern systems like ERP and WMS automate order processing with real-time inventory updates. Upon receipt, systems automatically confirm orders, check stock availability, and generate picking lists, improving speed while reducing errors.
Employee training is essential to handle complex orders. Customer feedback should guide continuous process improvements to meet evolving market needs.
5. Order Picking
Picking efficiency significantly affects customer satisfaction and profitability. Picking methods should be selected based on warehouse size, product types, and order volumes.
Common approaches include discrete order picking, batch picking, zone picking, and wave picking. Discrete picking suits small operations, while batch picking handles high volumes. Zone picking divides warehouses into sections, and wave picking groups similar orders.
Warehouse layouts should minimize picker travel time. Barcode or RFID technologies reduce errors. Employee training and incentive programs further enhance picking productivity.
6. Packaging and Shipping
Final packaging and shipping affect product safety and customer satisfaction. This stage includes order consolidation, quality checks, packaging, labeling, and transportation coordination.
Packaging materials and methods should match product characteristics, shipping methods, and customer requirements. Fragile items need reinforced packaging. Automated packaging equipment improves efficiency and reduces errors. Accurate labeling ensures proper routing.
Final quality checks prevent shipping errors. Close coordination with carriers ensures timely deliveries. System integration with transportation providers enables shipment tracking for on-time fulfillment.
II. Process Execution, Monitoring, and Improvement
Standard Operating Procedures (SOPs) and Key Performance Indicators (KPIs) ensure efficient process execution. SOPs establish operational standards to reduce variability, while KPIs measure success across metrics like storage costs, inventory turnover, picking accuracy, and on-time shipments.
Regular KPI analysis identifies bottlenecks for targeted improvements. Continuous enhancement through value stream analysis and PDCA (Plan-Do-Check-Act) cycles eliminates non-value-added activities and optimizes workflows.
III. The Critical Role of Workforce Management
Employees execute operations while monitoring quality and providing feedback. Effective human resource management boosts satisfaction and motivation, driving operational improvements.
Training programs should enhance technical skills and safety awareness. Incentive systems encourage innovative suggestions. Open communication fosters collaboration across departments, improving overall efficiency.
In conclusion, optimizing warehouse operations is essential for logistics efficiency, cost reduction, and competitive advantage. By enhancing process management and integrating advanced technologies, companies can set new industry benchmarks. This discussion aims to inspire excellence in warehouse management for superior business performance.