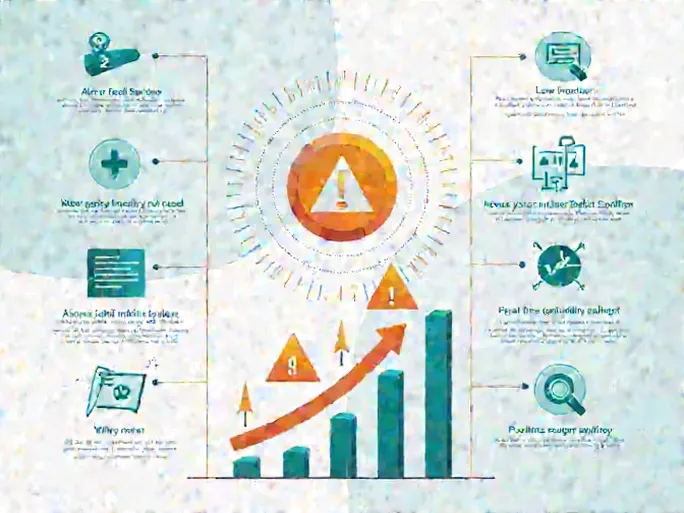
In today's rapidly evolving market landscape, businesses face unprecedented challenges in meeting customer demands while effectively managing inventory. Inventory management directly impacts a company's financial liquidity, operational efficiency, and ultimately, customer satisfaction and competitive advantage. To address these challenges, an increasing number of enterprises are prioritizing the implementation of inventory alert systems—a core tool for optimizing inventory management. This article examines the necessity of inventory alert mechanisms, their construction process, implementation outcomes, and real-world applications through case studies.
I. The Necessity of Inventory Alert Systems
The primary purpose of an inventory alert system is to monitor stock levels in real-time through data analysis and predictive modeling, enabling early detection of potential issues. This approach allows businesses to respond effectively to market fluctuations while minimizing inventory-related risks. Inventory represents not only a significant corporate asset but also a critical factor influencing operational efficiency and cost structure. Excessive inventory levels can tie up working capital, impairing liquidity and resource allocation, while insufficient stock may result in shortages that damage customer satisfaction and brand reputation. Therefore, implementing an inventory alert system serves as the crucial balancing mechanism.
1.1 Establishing Quantitative Metrics
When developing an inventory alert system, companies must define clear warning indicators. These metrics—including but not limited to inventory turnover rates, stockout frequency, and carrying costs—help quantify inventory status. By monitoring these indicators, organizations gain precise visibility into current stock conditions and can make data-driven decisions. For instance, low inventory turnover may signal overstocking, prompting consideration of reduced purchasing or promotional activities to accelerate sales.
1.2 Real-Time Data Monitoring
Continuous data monitoring forms the backbone of effective inventory alert systems. Through modern information technologies like Enterprise Resource Planning (ERP) and Warehouse Management Systems (WMS), businesses can automate inventory data collection and analysis. This capability enables real-time tracking of stock movements and swift operational adjustments. The immediacy of data ensures decision-makers operate with current information, significantly reducing response delays.
II. Constructing an Inventory Alert System
Building a comprehensive inventory alert mechanism requires multiple implementation phases: defining metrics, establishing warning models, collecting and analyzing data, followed by system integration and optimization.
2.1 Defining Alert Parameters and Thresholds
The initial step involves setting appropriate alert indicators and thresholds tailored to operational characteristics and industry standards. These parameters should accurately reflect inventory status while aligning with business objectives. For example, companies might establish stock thresholds based on product lifecycles, seasonal demand patterns, and market trends. When inventory levels breach predefined limits, the system automatically triggers alerts to prompt managerial action.
2.2 Developing Predictive Models
Following metric definition, organizations must construct forecasting models. Typically leveraging historical data analysis through time-series algorithms or machine learning techniques, these models predict future inventory requirements. By incorporating sales data, market demand, and seasonal variations into the modeling process, companies achieve more accurate stock projections, thereby reducing carrying risks.
2.3 Data Collection and Analysis
Effective data collection and interpretation form the foundation of reliable alert systems. Modern IT solutions enable efficient gathering of inventory-related information, including sales figures, procurement data, and customer feedback. Advanced analytics and data mining techniques help identify underlying trends, facilitating early problem detection while providing empirical support for strategic decisions.
2.4 System Integration and Process Refinement
The final implementation phase involves integrating the alert mechanism with existing management platforms. Companies must ensure seamless interaction between inventory alerts and other business functions—procurement, sales, production—to create closed-loop operational processes. Through continuous monitoring and evaluation, organizations can iteratively refine warning protocols, developing agile, adaptive management frameworks.
III. Case Study: Electronics Manufacturer's Implementation Success
To illustrate practical applications, we examine how a consumer electronics manufacturer successfully optimized inventory management through alert systems, navigating raw material price volatility and demand uncertainty.
3.1 Initial Challenges
Prior to implementation, the company faced significant inventory management difficulties. Without robust data monitoring, the organization frequently encountered overstock situations or product shortages. Excessive inventory tied up substantial capital, while stockouts negatively impacted customer experiences, creating sales decline risks.
3.2 System Deployment
Recognizing these operational threats, the manufacturer implemented an inventory alert system to enhance stock control. The initiative began with defining key metrics—inventory turnover, average days in stock, and stockout rates—while utilizing ERP systems for real-time data tracking and model development.
3.3 Measurable Outcomes
Post-implementation results demonstrated marked improvement. Dynamic threshold adjustments enabled rapid response to market conditions, reducing capital allocation by 18%. Inventory turnover increased 20%, while stockout rates fell below 5%, significantly boosting customer satisfaction. These enhancements strengthened overall supply chain efficiency, resolving inventory issues while establishing foundations for sustainable growth.
IV. Future Developments and Challenges
Despite proven effectiveness, inventory alert systems face implementation barriers including data quality issues, demand unpredictability, and internal coordination gaps. Looking ahead, advancements in big data analytics and artificial intelligence promise system enhancements. Organizations must monitor technological progress while strengthening data management capabilities to maintain competitive positioning in complex market environments.
In conclusion, robust inventory alert mechanisms represent essential tools for modern enterprises confronting market complexities. Through scientific metric design, flexible threshold configuration, and efficient response protocols, businesses can navigate volatile demand landscapes while achieving operational sustainability. Though implementation challenges exist, continuous process optimization and data management improvements will ensure organizational resilience. As technology evolves, inventory alert systems will continue delivering strategic value, presenting both opportunities and challenges for forward-thinking enterprises.