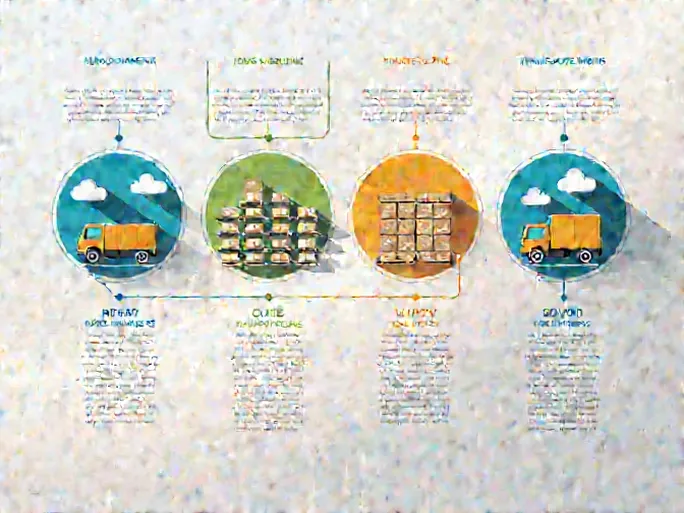
In contemporary logistics operations, warehouse signage plays an indispensable role. An effective labeling system not only enhances operational efficiency but serves as the cornerstone of seamless warehouse management. Imagine a facility where neither goods nor storage locations bear any identification—how would employees quickly locate needed items? Such disorganization would waste valuable time, increase error rates, and ultimately raise operational costs. This examination explores the planning and implementation of warehouse signage, covering various types, design requirements, and execution standards to ensure efficient and accurate warehouse operations.
The Diversity and Significance of Warehouse Signage
Modern warehouses utilize several distinct signage types, each serving specific functions that collectively create a comprehensive information system.
1. Floor Markings
As the most visible component, floor markings primarily delineate zones and distinguish pallet locations, enabling staff to quickly identify different operational areas. Color-coded flooring, for instance, can clearly demarcate receiving zones, picking areas, and outbound staging sections.
However, floor markings present limitations. Positioned at ground level, they risk obstruction by movable goods or equipment and may fade from wear. Critical areas should combine floor markings with wall or rack signage to ensure visibility.
2. Wall Signage
Positioned at eye level, wall signage offers superior visibility for area demarcation, operational instructions, and safety warnings. A "No Entry" sign near forklift pathways, for example, enhances safety awareness.
Effective wall signage prioritizes clarity and color contrast. Overly complex designs or small fonts create reading difficulties, undermining efficiency. Simple, standardized designs with uniform typography maximize comprehension.
3. Rack Labels
Essential for storage management, rack labels display location codes, item numbers, product names, and quantities. Limited space demands concise information presentation—overly detailed labels confuse rather than guide.
Innovative solutions like QR codes complement traditional labels, enabling staff to rapidly access product details and streamline picking processes.
4. Product Identification
Item-specific labels distinguish between products or different batches within categories. Color-coding creates visual differentiation—red tags might indicate near-expiry goods while green denotes fresh stock, enabling intuitive identification and process optimization.
5. Visual Communication Efficiency
Effective signage balances immediate visibility with management functionality. Overly verbose labels create confusion, whereas standardized symbols or photographic examples enhance comprehension. Pictorial "No Entry" or "Caution" signs, for instance, communicate faster than text-heavy warnings, helping staff acclimate to work environments.
Standardization and Unified Signage Systems
Consistency across signage dimensions, colors, fonts, and imagery establishes professionalism while reducing staff confusion. Comprehensive documentation of operational, management, and signage standards accelerates new employee onboarding and improves overall efficiency.
Implementing daily inspection protocols ensures signage remains legible and intact, minimizing errors from deteriorated labels. Regular training reinforces proper signage interpretation and safety awareness.
Operational Efficiency Through Strategic Signage
Beyond aesthetics, optimized signage directly enhances productivity. During order picking, well-designed labels guide workers to prioritize same-pallet items, smoothing outbound processes. Clearly marked restricted areas prevent operational errors, while barcode systems integrated with location signage minimize manual search time.
Data analysis of picking patterns and error rates informs continuous signage improvements, creating feedback loops that refine warehouse workflows. When employees access accurate information swiftly, job satisfaction rises while operational risks decline.
Continuous Optimization and Implementation
Warehouse signage systems require ongoing evolution to meet changing operational needs. Each logistics stage benefits from thoughtful identification solutions that boost efficiency. Material innovations—like wear-resistant floor markings and high-definition product labels—extend signage longevity.
Ultimately, signage transcends visual markers to become integral to warehouse operations. Systematic refinement of identification systems delivers substantial productivity gains and cost reductions. By embedding signage considerations throughout all management processes, facilities achieve the dual objectives of enhanced efficiency and optimized expenditures—a competitive advantage in today's logistics landscape.