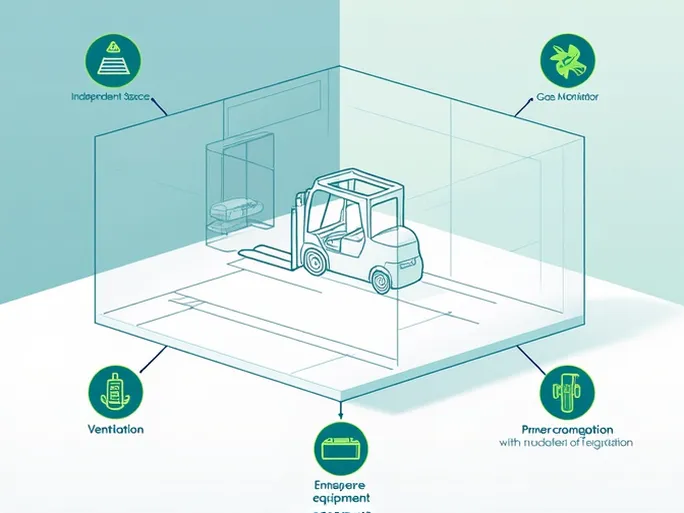
In today's logistics industry, forklifts have become indispensable equipment. They not only enhance material handling efficiency but also directly impact warehouse operational fluidity. However, optimal forklift performance depends not just on operator skills—proper charging management is equally critical.
Electric forklifts can deliver superior endurance and performance in daily operations, provided their charging processes maintain strict compliance. Neglecting proper charging station protocols may lead to significant safety hazards and potential business losses. Industry surveys reveal that 80% of warehouses exhibit varying degrees of non-compliance in forklift charging management—a warning that demands immediate attention. Warehouse managers must prioritize charging station compliance across these seven key areas.
1. Dedicated Space: The Primary Safety Barrier
A segregated charging area represents both a legal requirement and a fundamental safety measure. Fire safety regulations mandate that forklift charging stations occupy isolated spaces separate from storage areas, with proper fire barriers. This design minimizes environmental interference during charging and reduces fire risks.
Locating charging stations within warehouse interiors poses dual threats: potential hazardous gas exposure across operational zones and the risk of cascading operational disruptions during incidents. Proper charging facilities should feature explosion-proof pressure relief roofing and reinforced concrete or steel framing to contain potential accidents and protect adjacent areas.
2. Electrical Capacity: Safe Power Configuration
Appropriate electrical infrastructure forms the foundation of safe charging operations. Warehouse planners must select proper cable specifications during construction based on projected power demands. Continuous monitoring and adjustment of electrical loads prevents dangerous overload situations that could lead to short circuits or fires—events that disrupt operations and damage equipment.
Regular professional inspections of electrical systems help maintain safety standards, identify potential overload issues, and ensure stable power delivery to charging stations.
3. Gas Monitoring: Real-Time Hazard Detection
Many electric forklifts utilize lead-acid batteries that emit hydrogen during charging—a potentially explosive gas when concentrations exceed safe levels. Installing continuous gas monitoring systems with alarm capabilities provides critical early warning of dangerous gas accumulation. These systems should trigger evacuation alerts when detecting hazardous hydrogen levels, allowing timely intervention before incidents occur.
4. Forced Ventilation: Maintaining Air Quality
The interaction between oxygen and toxic gases during charging necessitates robust ventilation systems. Electrical safety standards require lead-acid battery charging areas to maintain minimum air exchange rates of eight cycles per hour. Regular maintenance of ventilation equipment ensures consistent performance in controlling harmful gas concentrations and protecting worker health.
5. Explosion-Proof Outlets: Enhanced Electrical Safety
Specialized explosion-proof outlets represent essential equipment for charging areas. Their aluminum alloy construction provides corrosion resistance and structural durability, while internally protected electrical components prevent ignition of surrounding gases. Implementing these safety-rated devices demonstrates compliance with regulations and commitment to worker protection.
6. Fire Suppression: Essential Emergency Preparedness
Charging stations must comply with GB50140 standards for fire extinguisher placement. Gas leaks during charging create significant fire risks, making proper extinguisher selection critical. Recommended solutions include ammonium phosphate dry chemical and carbon dioxide extinguishers, specifically effective against gas-related fires. Regular inspection and maintenance ensure emergency equipment remains operational when needed.
7. Supplementary Equipment: Comprehensive Safety Infrastructure
Complete charging station safety requires supporting equipment like electric hoists and emergency eyewash stations. Hoists facilitate safe movement of heavy lead-acid batteries, preventing worker injuries, while eyewash stations provide immediate response capability for electrolyte exposure incidents. These complementary systems significantly enhance overall warehouse safety management.
Conclusion: Synergizing Safety and Efficiency
Compliant forklift charging operations contribute to both warehouse safety and supply chain efficiency. As risk management awareness grows industry-wide, warehouse managers must integrate charging station protocols into daily safety systems. Through facility improvements, rigorous management, and targeted training, warehouses can achieve the dual objectives of operational safety and productivity—foundational elements for success in today's competitive logistics environment.
Prioritizing safety-focused, efficiency-driven compliance measures for forklift charging stations creates substantial business value while establishing resilient operational frameworks for future challenges.