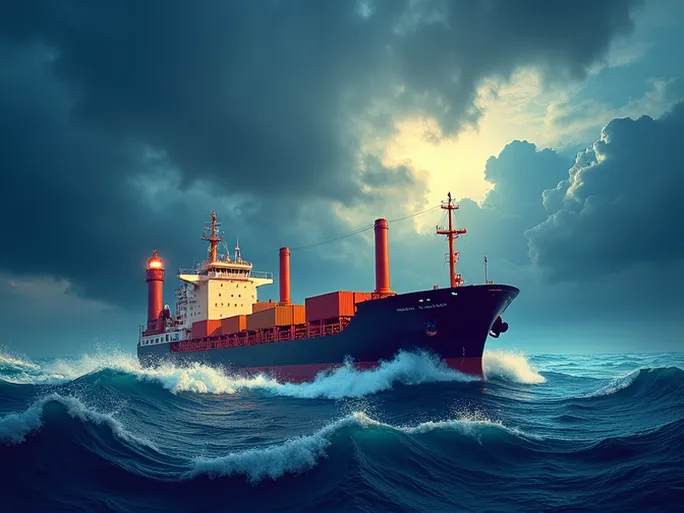
In global trade, maritime shipping plays a pivotal role, accounting for over 80% of transported goods. However, recent multiple shocks—including the pandemic, extreme weather events, geopolitical tensions, labor disputes, and trade barriers—have severely disrupted this critical transportation system. According to maritime analysis firm Sea-Intelligence, schedule reliability in 2024 stands at just 50-55%, making supply chain resilience and reliability top priorities for shippers.
But what exactly are the consequences of unreliable shipping for businesses? And how can shippers mitigate these impacts?
Defining Reliability in Maritime Shipping
In shipping, reliability means maintaining stable and trustworthy schedules while delivering end-to-end service that meets customer requirements. This encompasses several critical factors:
- Providing high-quality equipment
- Ensuring on-time departures and arrivals
- Maintaining accurate documentation
- Guaranteeing safety throughout transit to prevent damage or loss of personnel, plants, or equipment
- Sustaining consistent communication and transparency during transportation
When executed properly, these elements enable smoother operations, reduce costs, and enhance customer satisfaction. However, failures in any aspect can significantly impact shippers' businesses.
The High Cost of Unreliable Shipping
An AlixPartners survey of 570 global logistics decision-makers revealed that 76% consider financial resilience in logistics crucial for their companies—a growing industry trend. Yet a single port delay often triggers supply chain ripple effects, substantially increasing costs for both shippers and terminal operators.
The financial, operational, and reputational consequences of unreliable shipping can jeopardize shippers' financial resilience—their ability to maintain profitability in an increasingly volatile global environment. Key impacts include:
Financial Impacts: Increased operational and inventory costs, lost sales, penalties and additional fees, and higher working capital requirements.
Operational Impacts: Production line disruptions, along with the complexity and costs of implementing contingency plans.
Reputational Impacts: Loss of sales and market share, deteriorating profit margins, reduced customer satisfaction and loyalty, and damage to corporate reputation.
Building Resilience Against Disruptions
In AlixPartners' recent Disruption Index survey, nearly half of business executives anticipated more severe supply chain disruptions this year than last. Fortunately, shippers can adopt several strategies to reduce disruption risks and adapt quickly when reliability falters:
- Leverage data when evaluating logistics partners
- Partner with integrated logistics providers managing multiple supply chain domains
- Clearly define service reliability expectations
- Plan ahead to eliminate risks from controllable or known factors
- Diversify shipments across different transportation modes (air, rail, road, etc.)
- Invest in technology
- Establish contingency plans
- Monitor industry news to stay informed about potential disruptions
By implementing these effective strategies, shippers can not only strengthen their supply chain resilience but also stabilize their market position and customer relationships amid uncertainty.