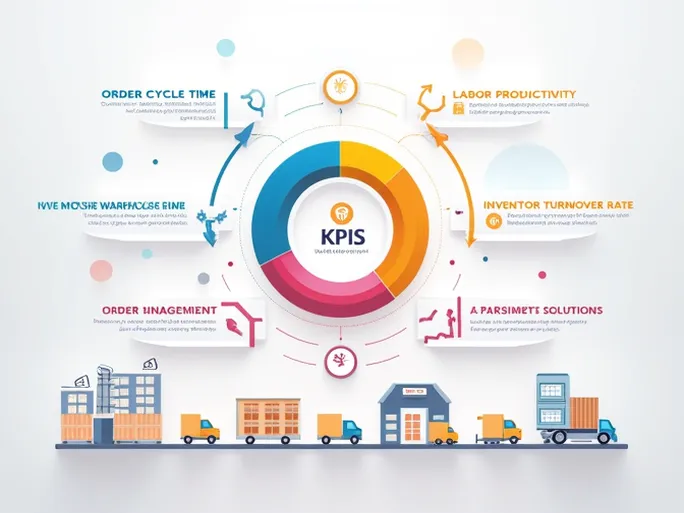
In today's rapidly evolving business landscape, the ability to quickly and accurately meet customer demands has become crucial for sustainable growth. An efficient order fulfillment process not only impacts operational effectiveness but directly determines customer satisfaction and loyalty. Every step of this process—from order receipt and processing to final delivery—requires meticulous attention to detail and continuous optimization. This article provides professional guidance and practical techniques to enhance your order fulfillment efficiency, helping your business stand out in today's competitive market.
Enhancing Order Fulfillment Efficiency: Key Performance Indicators
Improving order fulfillment efficiency begins with understanding key performance indicators (KPIs). Analyzing each operational segment helps businesses implement targeted improvements. These KPIs encompass fulfillment costs, cycle time, labor productivity, picking accuracy, return rates, and inventory turnover—all critical metrics for strategic planning and daily operations.
1. Fulfillment Costs
Fulfillment expenses significantly impact profitability. Businesses should track all costs associated with inventory receipt, storage, packaging, and transportation to establish proper budgeting and control measures. When specific cost areas show abnormal increases, immediate analysis and optimization are necessary—for example, collaborating with supply chain partners to secure competitive shipping rates and reduce transportation expenses.
2. Order Cycle Time
Order cycle time measures the duration from customer purchase to product delivery. Optimizing internal workflows to eliminate unnecessary delays can significantly reduce this timeframe. Implementing real-time order tracking systems ensures prompt responses and enhances customer experience. Regular process evaluations to identify bottlenecks also effectively shorten cycle times.
3. Labor Productivity
Employee productivity directly affects operational costs. Implementing performance-based incentive systems that combine base salaries with bonuses can boost motivation. Equally important is investing in employee training to enhance skills and work efficiency.
4. Order Picking Accuracy
Picking accuracy directly influences customer satisfaction. Technologies like barcode scanning and RFID minimize human errors, while continuous process optimization and system training further reduce mistakes.
5. Return Rates
High return rates damage customer experience and create financial losses. Regular analysis of return reasons—whether product quality issues, inaccurate descriptions, or shipping problems—enables targeted improvements. Proactive customer communication helps address issues at their source.
6. Inventory Turnover
This metric reflects inventory management effectiveness. Balancing supply with demand prevents overstocking or shortages. Implementing lean inventory practices and dynamic forecasting models optimizes stock levels.
Thorough analysis of these KPIs helps identify inefficiencies and develop appropriate solutions. The following seven optimization techniques provide actionable implementation strategies.
Seven Optimization Techniques
1. Warehouse Layout Optimization
An efficient warehouse design maximizes space utilization, reduces transportation costs, and improves operations. Strategic zoning with high-demand items stored near picking areas saves time. Vertical storage solutions leverage three-dimensional space, lowering storage costs while improving accessibility.
2. Real-Time Inventory Management
Live inventory monitoring prevents stockouts or excess inventory. Robust tracking systems maintain accurate, up-to-date data while safety stock levels accommodate demand fluctuations, enhancing customer satisfaction.
3. Strategic Storage Location Planning
Analyzing picking frequency and product characteristics enables optimal storage placement. Regular adjustments based on demand changes ensure easy access to popular items, minimizing worker movement. Information management systems can visualize picking paths for greater efficiency.
4. Streamlined Picking Processes
Simplified picking significantly boosts fulfillment speed. Wave picking suits large volumes of similar orders, while zone picking better handles diverse orders by allocating resources precisely.
5. Efficient Packaging and Shipping
Automated packaging reduces errors and increases speed. When selecting carriers, evaluate both cost and delivery performance to ensure timely shipments. Regular vendor assessments maintain service quality.
6. Advanced Tracking Technologies
Real-time order tracking systems improve transparency and customer experience. Data analytics tools uncover market trends and customer preferences, supporting data-driven decision making.
7. Clear Communication Channels
Effective interdepartmental communication prevents information gaps. Centralized platforms enable real-time updates, particularly valuable for complex orders, reducing errors and improving fulfillment outcomes.
Strategic Implementation
Beyond operational improvements, businesses should adopt data-driven decision making, using analytics to predict demand and adjust strategies. Building flexible fulfillment capabilities allows quick adaptation to market changes. Reverse logistics optimization—managing returns efficiently—reduces losses while providing insights for product and service enhancements.
Investing in employee training and motivation is equally vital. Comprehensive training programs build skills and teamwork, while performance incentives maximize individual contributions, collectively boosting organizational performance.
Each optimization step contributes to long-term success. Continuous improvement not only enhances fulfillment efficiency but strengthens brand reputation—yielding both financial gains and customer trust. Through systematic analysis, strategic implementation, and persistent effort, businesses can achieve sustainable growth in today's competitive environment.