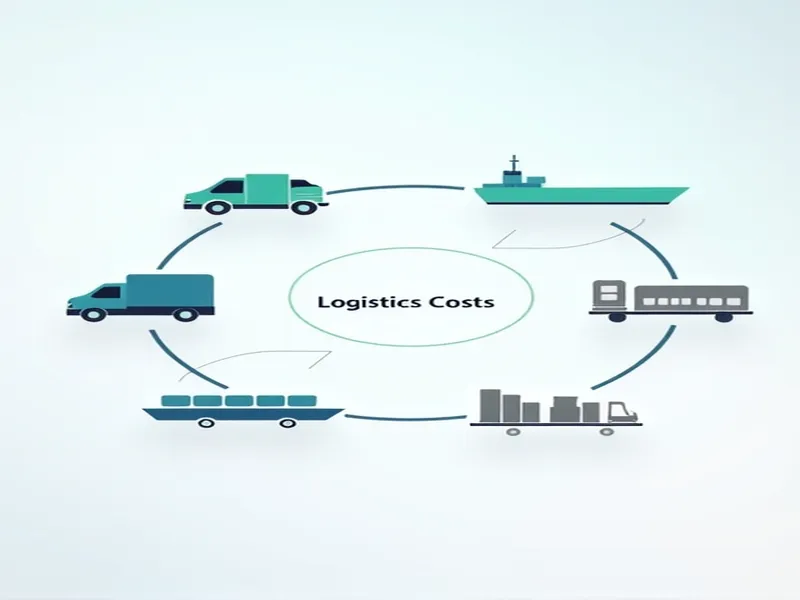
In today's rapidly developing economy, the importance of the logistics industry has become increasingly prominent. With the advancement of globalization and intensifying market competition, while pursuing profit maximization, enterprises must pay full attention to logistics cost management. Logistics costs are not merely an operational expense—they represent a crucial factor determining a company's profitability and market competitiveness. Therefore, how to scientifically and reasonably calculate and control logistics costs has become a common challenge for every business seeking to establish itself in the market.
Understanding Logistics Cost Components
First, we must understand the composition of logistics costs, which can be divided into three main parts:
- Direct operational costs: These include transportation fees, warehousing costs, loading/unloading expenses, and other fees directly related to physical goods movement. These unavoidable operational expenses directly impact overall profitability when properly controlled.
- Information processing costs: While less visible than transportation costs, expenses for logistics information transmission and processing play a vital role in ensuring smooth, efficient operations. These investments in information systems and data processing facilities can, over time, improve information flow efficiency and reduce overall logistics costs.
- Comprehensive management costs: To maintain smooth logistics operations, companies implement various management measures involving human resources, system development, and other layered investments. Accurate logistics cost calculation must account for both visible expenses and hidden costs embedded throughout the process.
Key Considerations for Logistics Cost Calculation
Several critical conditions must be established when calculating logistics costs:
1. Defining logistics scope: The boundaries determining a product's origin and destination affect the entire cost structure. For example, transportation from suppliers to factories, internal material transfers, factory-to-warehouse logistics, and final customer deliveries all constitute essential logistics cost components. After defining the scope, companies should properly evaluate each segment's cost structure for more accurate data.
2. Selecting appropriate functional scope: Logistics functions extend beyond transportation to include storage, distribution, packaging, and loading/unloading. Different functional combinations directly impact cost calculations. For instance, outsourcing certain segments might reduce costs, but success depends on the cost difference between outsourcing and in-house operations. Companies must carefully analyze how various options affect costs when designing logistics systems.
3. Accounting for all cost categories: Both internal and external expenses—including freight, storage fees, and labor costs—should be properly included. Clearly defining these categories is crucial for subsequent cost control and decision-making. Many companies overlook hidden costs during calculations, resulting in inaccurate data that leads to poor decisions. Comprehensive consideration of all expenses ensures accurate logistics cost reflection.
Optimizing Logistics Cost Control
Effective cost control requires scientific methodologies. Companies should focus on optimizing logistics processes by improving each segment's efficiency to reduce costs. Potential strategies include:
- Implementing modern information technology to optimize transportation routes and eliminate unnecessary segments
- Using precise data analysis tools for inventory management to reduce stagnant goods storage costs
- Negotiating favorable transportation and procurement terms with suppliers
Establishing robust information feedback mechanisms also helps control logistics costs. By monitoring operations in real-time, companies can quickly identify and resolve issues while tracking cost fluctuations. This approach improves logistics transparency, enables timely strategy adjustments, enhances customer satisfaction, and ultimately strengthens market competitiveness.
Conclusion
Logistics cost management and control represent an ongoing optimization process rather than a one-time achievement. Companies must establish scientific cost accounting systems, properly plan logistics networks, and leverage modern technology for process optimization and efficiency improvement. Through these comprehensive efforts, businesses can truly reduce costs while enhancing operational efficiency for sustainable development. In tomorrow's commercial ecosystem, mastery of logistics cost control will determine who holds market initiative and gains broader development opportunities.