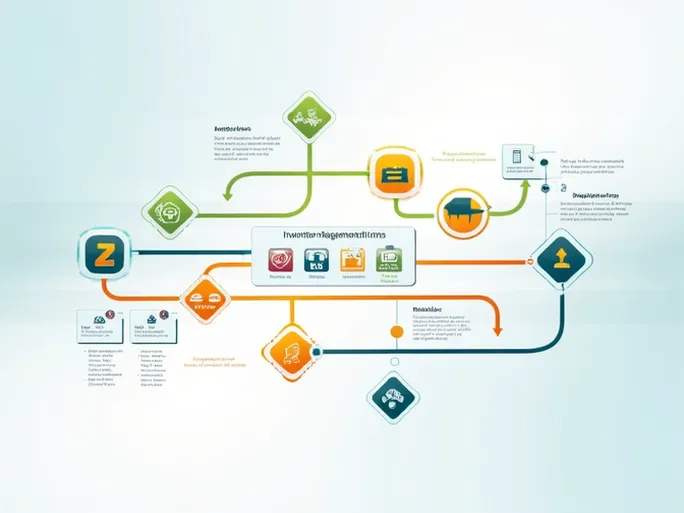
In the context of modern supply chain management, businesses face numerous challenges, particularly in inventory management. Effective inventory control serves as a crucial component for enhancing competitiveness, reducing costs, and meeting customer demands. However, traditional inventory management models often struggle to adapt to rapidly changing market conditions, leaving companies ill-equipped to handle demand fluctuations and supply instability. In this environment, joint inventory management has emerged as an innovative strategy, gaining attention as a vital tool for optimizing stock levels and improving efficiency in contemporary supply chains.
Traditional supply chain management often suffers from fragmented operations. Suppliers, manufacturers, and retailers typically operate with minimal communication and information sharing, resulting in disparate inventory strategies and standards. This lack of coordination leads to delayed responses to demand changes, exacerbating information distortion—a phenomenon known as the "bullwhip effect." As demand signals amplify progressively through the supply chain, market volatility intensifies, increasing inventory risks for all parties. Joint inventory management addresses these complexities by facilitating resource integration and information sharing, enabling more efficient inventory control.
The Importance and Advantages of Joint Inventory Management
At its core, joint inventory management focuses on integrating upstream and downstream supply chain operations to promote information sharing and collaborative efforts, ultimately optimizing inventory levels and reducing costs. This approach offers several significant benefits:
- Real-time information sharing enables participants to monitor demand fluctuations and adjust inventory strategies promptly, preventing stock imbalances caused by data delays.
- By minimizing data inconsistencies, companies can reduce excess inventory and free up working capital, gaining a competitive edge in the market.
- The strategy helps lower inventory levels, decrease overproduction, and optimize production schedules, systematically reducing logistics costs while improving overall operational efficiency.
- Implementation often strengthens inter-company relationships, expanding the scope and depth of collaboration to facilitate resource sharing and risk mitigation.
Implementation Pathways for Joint Inventory Management
Successful adoption of joint inventory management requires clear implementation roadmaps and specific actions. Key steps include:
- Establishing communication channels: Effective communication platforms are essential for real-time information exchange among suppliers, manufacturers, and retailers.
- Integrating information systems: Modern technologies like Electronic Data Interchange (EDI), barcode systems, and cloud computing enhance transparency and enable seamless data sharing.
- Building trust mechanisms: Mutual confidence forms the foundation of successful collaboration, achieved through contractual agreements, regular communication, and shared risk management.
- Creating win-win incentives: Equitable profit distribution mechanisms ensure all participants benefit from cooperation, motivating sustained commitment to optimization efforts.
Challenges in Joint Inventory Management
Despite its advantages, joint inventory management faces several practical challenges. Technological limitations in supplier-retailer coordination can lead to information asymmetry and communication barriers. Weak trust foundations may cause reluctance in data disclosure, while unfair benefit allocation can discourage deeper collaboration, limiting broader adoption of the strategy.
Case Study: Successful Implementation of Joint Inventory Management
A major supermarket chain's partnership with its suppliers illustrates the benefits of joint inventory management. Previously, suppliers managed inventory independently, resulting in excessive stock levels and frequent product shortages. After implementing joint inventory management, the supermarket established real-time data sharing with suppliers, enabling flexible production adjustments and inventory optimization. The partners also co-developed demand forecasting models, improving product turnover rates and strengthening market competitiveness. This case demonstrates how joint inventory management can enhance individual performance while driving overall supply chain improvement.
Conclusion
Joint inventory management represents a vital solution for addressing the complexities of modern supply chains. By integrating information sharing and collaborative processes, this strategy not only optimizes inventory control but also provides significant competitive advantages. As businesses navigate evolving market conditions, adopting joint inventory management will become increasingly important for maintaining competitiveness, improving service quality, and achieving sustainable growth. Companies should evaluate their current supply chain practices and develop clear implementation plans to successfully adopt this approach.