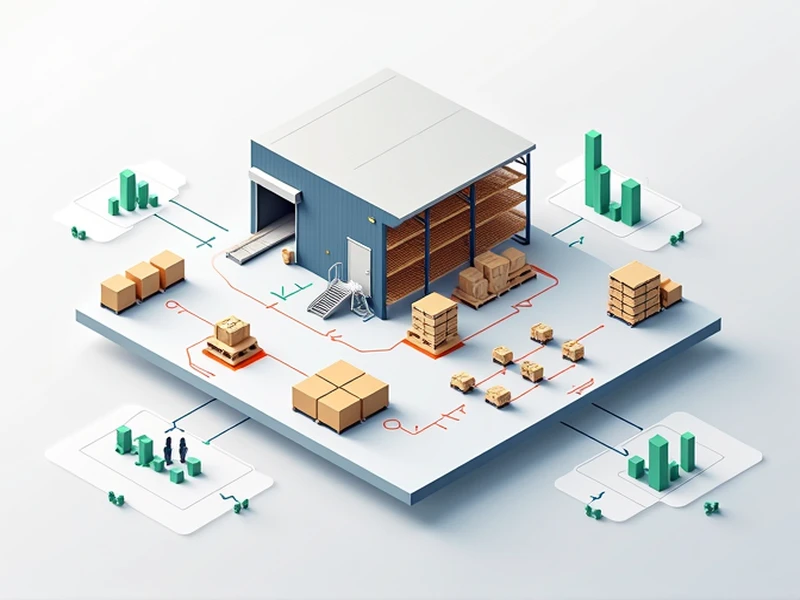
In today's logistics systems, warehouse management efficiency has become particularly crucial, impacting not only the smooth operation of the entire supply chain but also directly affecting corporate profitability. From a supply chain perspective, logistics operations represent a dynamic equilibrium between supply and demand. When this balance is disrupted—whether through production outpacing consumption or market demand exceeding available inventory—proper warehouse management becomes essential for maintaining equilibrium through strategic inventory reserves.
1. Dock Selection and Its Operational Impact
Warehouse selection, particularly in third-party logistics services, requires careful consideration of dock configuration. Facilities with loading docks are typically called "dock-high warehouses," which facilitate bulk cargo handling, while those without are termed "ground-level warehouses." In the automotive parts industry, for instance, ground-level warehouses dominate as they better suit operational workflows—forklift operators can directly load goods onto trucks without additional maneuvering, significantly improving efficiency. Conversely, dock-high warehouses may introduce unnecessary operational complexities like circuitous travel paths that reduce productivity.
Dock selection must align with product characteristics. Fast-moving consumer goods (FMCG), being compact and stackable, are ideally suited for dock-high warehouses where unloading can occur without forklift assistance. Poor dock selection can lead to substantial cost escalations, making close collaboration between warehouse managers and operations teams essential for optimal facility configuration.
2. The Strategic Importance of Racking Systems
Selecting appropriate warehouse racking systems represents another critical efficiency factor. Common options include beam racks, drive-in racks, and shuttle racks. For long-term contracts involving standardized goods, proper racking can dramatically improve storage density—where conventional floor storage wastes space, racking systems maximize cubic capacity.
However, beam racks aren't universally optimal. One FMCG client faced both overcrowding and inefficiency despite using beam racks exclusively. Analysis revealed their product characteristics actually favored drive-in or shuttle systems, which offer higher storage density and reduced aisle requirements. Data-driven racking redesigns can simultaneously minimize wasted space and accelerate order fulfillment.
3. Building Effective Performance Evaluation Systems
Employee performance metrics directly influence warehouse productivity. Well-designed evaluation systems motivate staff more effectively than egalitarian approaches that may encourage complacency. Human nature encompasses both self-interest and inertia, requiring performance programs that balance quantifiable individual metrics with team collaboration incentives.
Effective systems incorporate regular assessments, transparent results, and structured feedback sessions. Performance-based compensation reinforces motivation while addressing operational issues promptly. Teams lacking such mechanisms often experience productivity declines that ripple through entire operations.
In conclusion, warehouse efficiency depends less on supervision than on thoughtful system design. Strategic facility configuration, racking selection, and performance management collectively enhance operations while delivering measurable financial returns.