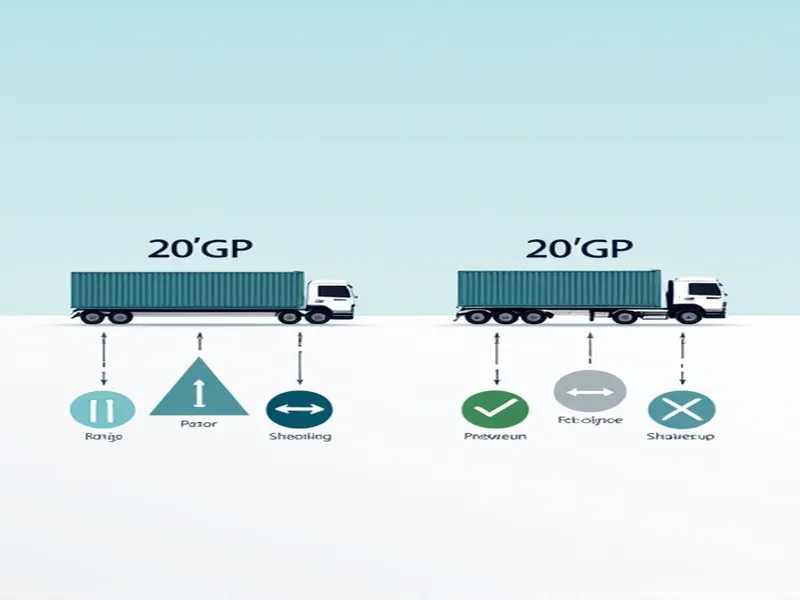
In the global freight system, containers serve as the standard transportation units, making knowledge of their weight limitations particularly crucial. Each container clearly displays its maximum weight (MAX WEIGHT XXXXKGS) and tare weight (TARE WEIGHT: ZZZZ KGS). These two figures allow shippers to easily calculate the maximum cargo weight, helping avoid losses and the hassle of reloading due to overweight containers.
Taking older model dry cargo containers as an example, 20'GP containers typically have a weight limit of 21.5 tons, making them suitable for heavy goods, while 40'GP containers are limited to 26 tons, better suited for lighter cargo. As container shipping has become more prevalent, even goods traditionally considered unsuitable for container transport are increasingly being shipped this way, driving innovation in container design. Specialized containers like the 40HQ, designed for lightweight goods, have a 25.5-ton limit. Furthermore, shipping companies have introduced reinforced container models for specific cargo types, such as 20'GP and 40'GP heavy-duty containers with limits of 27.5 tons and 28 tons respectively.
Key Factors Beyond Container Capacity
When considering container weight limits, several additional factors require attention:
- Port equipment limitations: Container handling at ports relies on cranes and forklifts. Overweight containers may exceed equipment capacity, particularly at smaller ports where weight restrictions are often communicated in advance.
- Road transport regulations: Countries like the United States and South Korea enforce strict road weight limits. Since many containers continue their journey by truck after unloading at ports, these road restrictions effectively become container weight limits.
- Shipping line capacity and balance: Container ships have limited space and weight capacity that don't always align perfectly. When demand for heavy cargo exceeds available space in certain regions, shipping companies may impose surcharges for overweight containers. In cooperative shipping arrangements, overweight containers may be refused entirely.
The Efficiency Challenge in Container Utilization
Understanding the complete container shipping process is key to improving efficiency and reducing costs. While proper container use can significantly enhance shipping efficiency, reality often falls short. A typical 20-foot container offers 33 cubic meters of space but averages only 25 cubic meters of actual use (about 75% utilization). Forty-foot containers fare slightly better with 67 cubic meters capacity typically holding 55 cubic meters of cargo (82% utilization).
Strategies for Improved Container Loading
Several approaches can enhance container loading efficiency:
- Optimized packaging design: Innovative packaging solutions can reduce volume and improve loading efficiency. Finding container-friendly shapes and adjusting box designs maximizes cargo capacity.
- Clear loading plans: Establishing effective communication channels between manufacturers, businesses, and container stations streamlines the loading process. Three-dimensional loading diagrams can effectively convey plans and boost operational efficiency.
- Standardized container databases: Creating comprehensive databases of various container specifications and successful loading cases enables more efficient packaging design and loading processes.
These technological innovations have already yielded significant improvements. Modern loading techniques have increased 20-foot container capacity to 30-33 cubic meters and 40-foot containers to 60-64 cubic meters, achieving 90%-96% utilization rates. Each container can now carry an additional 3-9 cubic meters of cargo, substantially reducing transportation costs.
With current shipping expenses at premium levels, proper planning and loading for each shipment can generate substantial savings. By optimizing container loading designs, businesses nationwide can improve container utilization rates during transportation, creating considerable economic benefits for all stakeholders.