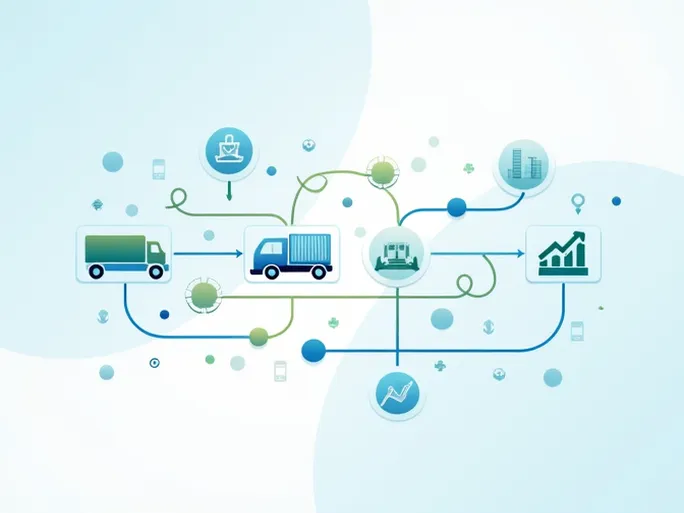
The volatility of economic conditions has profoundly impacted business operations, particularly during the current economic downturn where companies face unprecedented cost pressures and efficiency challenges. In this environment, developing systematic strategies to enhance operational efficiency and reduce logistics costs has become a critical priority for sustainable growth and competitive advantage.
1. Fundamentals of Supply Chain Management
Within corporate logistics cost reduction strategies, the Supply Chain Operations Reference (SCOR) model emphasizes the fundamental relationships between suppliers, companies, and customers. Modern enterprises typically establish multi-tier warehouse systems including:
- Global Distribution Centers (GDC)
- National Distribution Centers (NDC)
- Regional Distribution Centers (RDC)
These form the structural framework of internal supply chains. Core warehouse operations—receiving, storage, and shipping—rely on both physical resources (labor, space, equipment) and operational processes (systems, workflows, data management) to function effectively.
2. Comprehensive Business Diagnostics
To achieve meaningful logistics cost reductions, companies must transcend conventional operational perspectives and implement thorough business diagnostics. This requires:
- Weekly operational reviews to identify and resolve issues promptly
- Clear mapping of financial costs to their operational drivers
- In-depth analysis of key variables affecting cost structures
Warehouse cost optimization, for example, involves more than direct expense reduction—it requires holistic improvements in inventory management, procurement efficiency, and resource allocation.
3. Priority Identification and Method Selection
Effective cost reduction initiatives demand strategic focus on high-impact areas. Companies at different growth stages require distinct approaches:
- Startup phase: Prioritize market share expansion
- Contraction phase: Focus on service pricing optimization and requirement rationalization
Leadership teams must align cross-functional perspectives to develop tailored solutions for resource allocation and process optimization that deliver sustainable cost improvements.
4. Solution Development and Implementation
Root cause analysis using the "5 Whys" methodology provides the foundation for developing targeted solutions. Implementation success depends on:
- Rigorous project management
- Precise resource allocation
- Strict timeline adherence
Continuous monitoring of key performance indicators enables real-time strategy adjustments and ensures ongoing optimization throughout the implementation process.
5. Conclusion: Achieving Sustainable Efficiency
Successful cost reduction and efficiency improvement require balanced integration of:
- Technical expertise: For detailed operational improvements (ideal for experienced teams)
- Management systems: For comprehensive problem-solving (valuable for less-experienced organizations)
Through organizational restructuring and strategic external partnerships, companies can develop agile operational models that maintain competitiveness despite economic uncertainties.