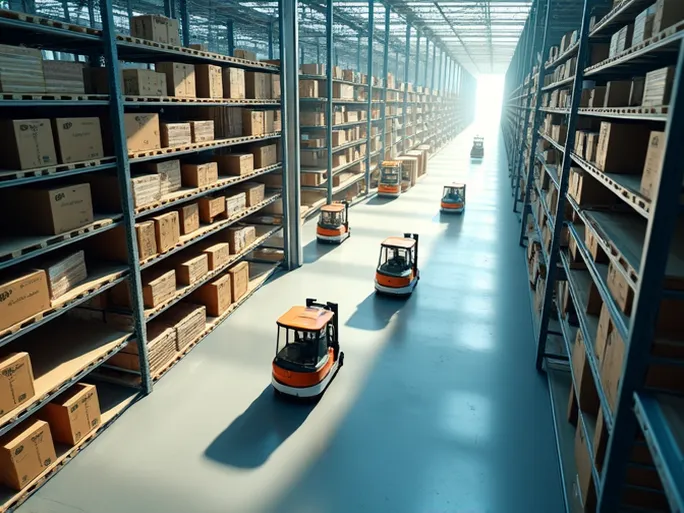
In today's industrial landscape, automated logistics is transforming traditional operations, particularly in large manufacturing enterprises where efficient workflow at every stage is crucial. Autonomous forklifts, with their efficiency, precision, and safety features, have become an indispensable part of modern smart logistics. But how exactly are these driverless vehicles revolutionizing material handling, and how will they shape the future of intelligent manufacturing?
1. Autonomous Forklifts: An Overview
Autonomous forklifts, also known as forklift AGVs (Automated Guided Vehicles), represent the core equipment of industrial automated logistics. Combining traditional forklift technology with AGV systems, these vehicles achieve unmanned material handling through advanced guidance technology and control algorithms. According to data from the New Strategy Robot Industry Research Institute and China Mobile Robot Industry Alliance, China's forklift AGV sales reached 2,700 units in 2019, an 80% year-on-year increase, with market size surpassing 1.3 billion yuan. This rapid growth clearly demonstrates the widespread demand and development potential of automated logistics solutions.
2. Advantages of Autonomous Forklifts
Compared to traditional forklifts, autonomous models offer multiple advantages:
- Enhanced Safety: Equipped with multiple safety features including emergency stop functions, automatic alarms, and object detectors, autonomous forklifts significantly reduce workplace accidents. Statistics show that forklift-related incidents cause approximately 20,000 serious injuries and fatalities annually in the United States alone - a number that autonomous systems can dramatically reduce.
- Reduced Operational Costs: Capable of 24/7 operation without human intervention, autonomous forklifts substantially improve efficiency and automation levels. Research indicates they can decrease warehousing costs by 30% while increasing gross profit by 7%. A single operator can manage multiple forklifts simultaneously, reducing labor requirements.
- Adaptability to Challenging Environments: Designed for flexibility, these vehicles can operate effectively in various demanding conditions including extreme temperatures and low-light areas, with robust obstacle avoidance capabilities.
- Scalability for Large Operations: Multiple autonomous forklifts can coordinate seamlessly in large-scale operations, meeting the automation and flexibility demands of modern production.
3. Comparative Analysis with Traditional Equipment
3.1 Manual Forklifts
Autonomous forklifts outperform their manual counterparts in safety, efficiency, and operational stability. Following pre-programmed routes, they automatically stop or reroute when encountering obstacles, eliminating risks associated with human error.
3.2 Traditional AGVs
In terms of load capacity and functionality, autonomous forklifts excel. While standard AGVs typically handle lighter loads, autonomous forklifts can manage over 2 tons while performing diverse operations including stacking and towing with greater efficiency.
3.3 Fully Automated Warehouses
Despite growing interest in fully automated storage systems, their high costs and inflexibility post-installation have made hybrid solutions combining autonomous forklifts with traditional racking increasingly popular. Hangcha Intelligent Technology, for instance, has successfully implemented such systems as efficient alternatives to fully automated warehouses.
4. Notable Implementation Cases
4.1 Chaoyang Tires
This prominent brand under Zhongce Rubber implemented 11 forklift AGVs to create a closed-loop smart logistics system in their workshop, achieving 24/7 autonomous operation that reduced labor costs while boosting efficiency.
4.2 Qingdao Sailun Group
In their smart factory spanning 77,000 square meters, Sailun deployed 53 reflectorless laser-guided forklift AGVs, driving intelligent transformation in tire manufacturing through advanced navigation technology.
4.3 Longxing Logistics
By integrating Hangcha AGVs with a hybrid dispatching system that interfaces with their WMS, Longxing optimized logistics operations, ensuring efficient unloading and container loading processes.
5. Future Development Trends
Looking ahead, autonomous forklifts will continue evolving toward greater intelligence and integration. Supported by emerging technologies like 5G, big data, and IoT, they will develop into multifunctional systems capable of intelligent decision-making and autonomous execution.
5.1 Increased Size and Speed: Future models will feature larger capacities and faster operating speeds while maintaining safety and reliability.
5.2 Enhanced Practicality and Lightweight Design: Improvements in durability and ease of operation will expand application scenarios, with cost controls ensuring economic viability.
5.3 Specialization and Standardization: Growing industry demands will drive development of specialized models alongside standardized solutions.
5.4 System Integration: Beyond individual unit performance, seamless integration with MES, ERP and other enterprise systems will create comprehensive, efficient production ecosystems.
As a cornerstone of modern industrial logistics, autonomous forklifts - with their efficiency, safety, and flexibility - are not only driving automation in manufacturing but accelerating the broader transition to intelligent production, establishing themselves as indispensable components of industrial progress.