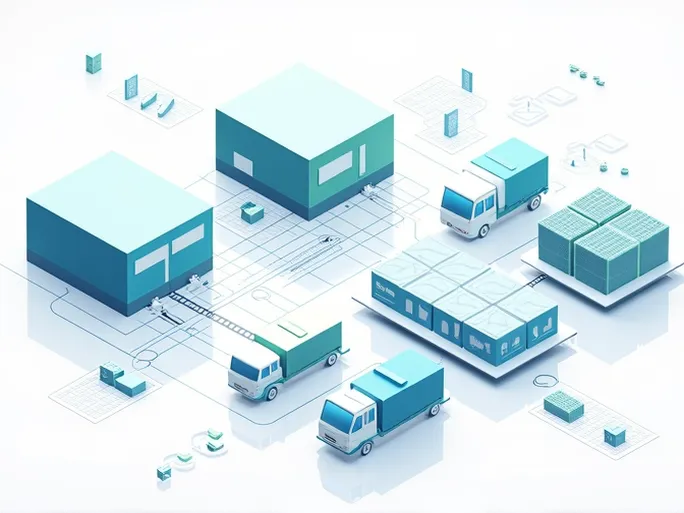
In an era where food safety and quality are increasingly prioritized, cold chain warehouse management has emerged as a crucial operational component for businesses. Among various logistics models, why has cold chain storage become particularly vital? The answer lies in its ability to preserve product quality by maintaining optimal temperature and humidity conditions, preventing deterioration and minimizing losses. As consumer expectations for food freshness and quality continue to rise, the professionalization and efficiency of cold chain storage have never been more important.
Cold chain warehousing represents more than just temperature-controlled facilities—it's a sophisticated system integrating refrigeration technology with freezing science. Within this system, any oversight can lead to significant quality degradation or even microbial growth, making precise environmental control essential.
1. Standardization and Unitization in Cold Chain Warehousing
The fundamental components of cold chain systems include pallets, racks, handling equipment, environmental monitoring systems, and management information systems. Standardized loading and integrated units serve as prerequisites for establishing cold chain storage benchmarks. During planning and design, particular attention must be paid to the standardization of these units, which proves critical for seamless interoperability between different cold chain operators.
When enterprises adopt identical standardized units for logistics operations, compatibility across the supply chain improves significantly. This standardization facilitates more efficient product flow and management while reducing time costs and material losses caused by equipment or system incompatibilities. Importantly, standardization should encompass both physical loading units and information management processes, with integrated IT solutions enhancing overall supply chain efficiency and responsiveness.
2. Key Control Factors in Cold Chain Storage Environments
Multiple elements influence cold chain storage effectiveness, including product characteristics, equipment, processing techniques, and operational management. Critical considerations include:
- Product Characteristics: Raw material quality and preservation requirements vary significantly by product. Research indicates that one hour of exposure to ambient temperatures can cause food quality deterioration equivalent to six months of storage at -20°C.
- Storage Equipment: High-quality refrigeration equipment forms the foundation of effective cold chain operations, with proper layout being equally important. Advanced monitoring systems now ensure strict compliance with temperature, humidity, and gas composition standards.
- Processing Techniques: Proper packaging, sanitation management, and processing methods are essential for maintaining optimal product conditions throughout storage and transportation.
- Human Factors: Well-designed operational procedures and responsive management systems help mitigate risks associated with manual handling.
- Biochemical Properties: Adjusting oxygen and carbon dioxide ratios according to product characteristics can extend shelf life and reduce spoilage risks.
3. Rack System Design and Planning
Storage efficiency depends heavily on well-designed rack systems that consider dimensions, connection methods, and structural configurations. Flexible layouts incorporating environmental monitoring nodes, lighting, and material handling systems can optimize both operational efficiency and product preservation.
Adaptable designs that accommodate diverse products and storage needs improve space utilization while standardized processes enhance inventory management efficiency.
4. Selecting Optimal Cold Chain Solutions
Cold chain logistics center performance depends fundamentally on functional zoning and equipment placement. Comprehensive analysis of product flow patterns helps identify high- and low-activity zones, enabling optimal space utilization.
Continuous process optimization based on product-specific requirements and temperature zone differences ensures increasingly scientific and efficient storage solutions.
5. Steel Rack Applications
Various steel rack configurations—including drive-in, push-back, and gravity-flow systems—are widely used in cold chain facilities. Proper selection can dramatically improve space utilization and turnover rates. For example, shuttle storage systems in 2,000m² warehouses can increase capacity by approximately 180% while reducing construction costs by 30%, significantly enhancing operational efficiency.
As technology advances, cold chain management stands poised for transformation through IoT, artificial intelligence, and big data applications. These innovations promise to elevate entire logistics systems to unprecedented levels of intelligence and efficiency.