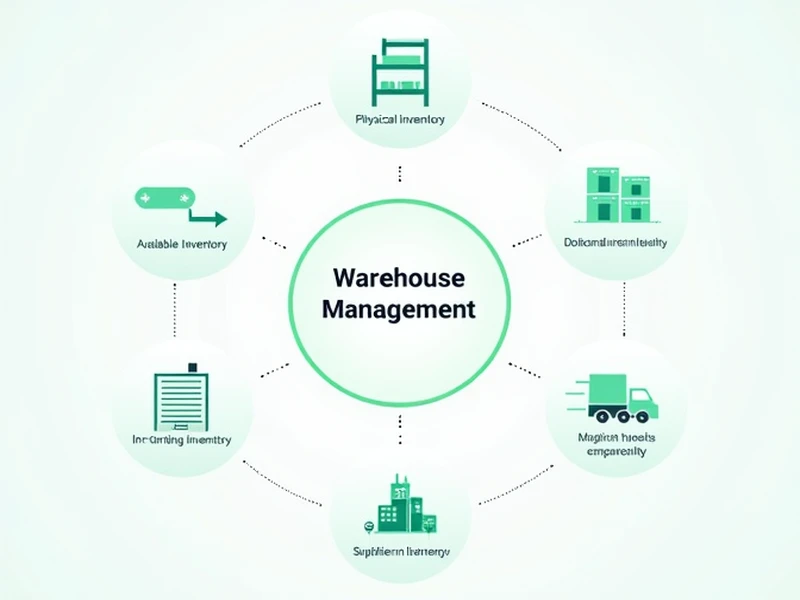
In warehouse management, efficient inventory control serves not only as a critical factor for enhancing operational efficiency but also as the foundation for supply chain optimization and cost reduction. Modern enterprises facing increasingly fierce market competition and volatile customer demands must implement refined inventory management to ensure each item can deliver maximum value at the right time and place. Clear inventory classification and data analysis have become indispensable components of this process. This article will explore the significance of different inventory types and their management strategies.
I. Physical Inventory Management
Physical inventory forms the operational backbone of warehousing. Enterprises must conduct regular stocktaking to maintain consistency between system records and actual quantities. Any discrepancies in physical inventory may lead to production delays, unfulfilled customer orders, and other serious consequences. Companies should establish robust inventory monitoring systems, utilizing technologies like RFID and barcodes for real-time tracking, enabling timely replenishment strategy adjustments to mitigate operational risks caused by information lag.
II. The Critical Role of Available Inventory
Available inventory directly impacts an enterprise's customer service capability. While its calculation appears straightforward, available inventory represents the core of upstream-downstream coordination. When order volumes exceed available stock, companies face pressure for emergency procurement or production—situations that not damage customer satisfaction but may incur additional transportation costs. Enterprises should employ predictive models and historical data analysis to establish appropriate safety stock levels, maintaining dynamic inventory management to respond to market fluctuations.
III. Inbound Inventory and Receiving Efficiency
Inbound inventory refers to goods that have arrived at the warehouse but haven't completed acceptance and storage processes. Companies must optimize receiving procedures by establishing standardized acceptance protocols and implementing advanced information management systems to ensure smooth GTP (Good To Process) workflow. Proper allocation of labor and equipment to reduce inbound cycle times can significantly enhance overall supply chain responsiveness.
IV. Risk Management for In-Transit Inventory
In-transit inventory—goods en route but not yet received—presents particular management complexity due to transportation time uncertainties that directly affect arrival schedules. Enterprises should maintain close communication with logistics providers, utilizing transportation management systems for real-time tracking to adjust production and shipping plans proactively, mitigating impacts from potential delays.
V. Supplier and Customer Inventory Considerations
Supplier and customer inventory management demands equal attention. Building strong partnerships with suppliers to encourage safety stock provisions or VMI (Vendor Managed Inventory) services can significantly improve supply chain resilience. For customer inventory, understanding consumption patterns enables better demand forecasting and personalized service offerings that strengthen customer retention.
VI. Optimizing Line-Side Inventory
Line-side inventory management proves especially crucial in manufacturing sectors. Properly managed line-side stock ensures production continuity while avoiding material idleness and waste. Companies should configure appropriate line-side inventory levels based on production schedules and material requirements, providing timely replenishment to maintain operational fluidity.
In conclusion, comprehensive understanding and effective management of diverse inventory types constitute the cornerstone for enhancing supply chain efficiency and reducing operational costs. When formulating inventory strategies, enterprises must holistically consider market demands, production capacity, supplier lead times, and other factors while leveraging data analytics for precise information sharing and coordination. However, manual management alone no longer suffices for complex inventory tasks—businesses urgently require AI, big data analytics, and other modern technologies to implement intelligent inventory management that elevates operational efficiency. Through systematic data analysis quantifying inventory fluctuation trends, companies can enhance decision-making rigor while maintaining competitive advantage to ensure sustainable profitability. Sound inventory management practices ultimately form the fundamental guarantee for corporate success.