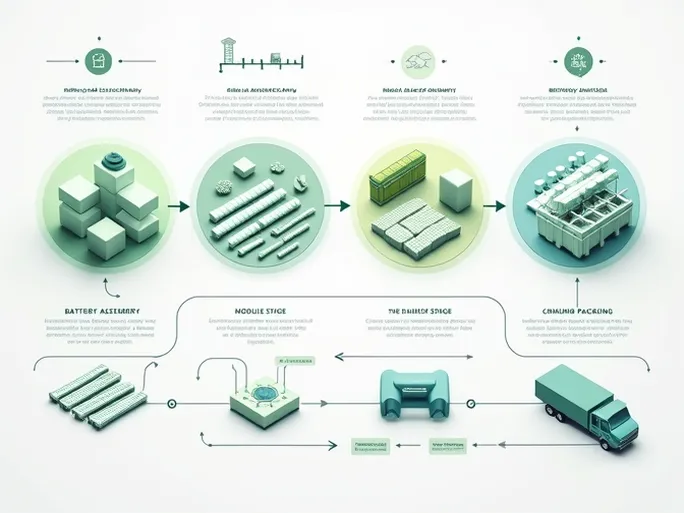
As electric vehicles (EVs) experience unprecedented growth worldwide, the battery logistics industry faces both tremendous opportunities and complex challenges. With global EV sales projected to exceed 27 million units by 2030—and lithium-ion batteries commanding nearly 70% of the market—establishing efficient, specialized supply chains has become mission-critical for every battery manufacturer.
The Four-Stage Battery Supply Chain
The lithium-ion battery supply chain comprises four distinct phases, each presenting unique logistical requirements:
1. Refining & Electrochemical Processing: At this initial stage, hazardous materials transportation becomes paramount. Specialized dangerous goods supply chains ensure raw materials reach manufacturing facilities both safely and efficiently, preventing production disruptions.
2. Battery Cell Production: Handling chemically sensitive components—including electrolytes, anodes, and cathodes—demands expert care. Even minor logistical errors during this phase can result in significant financial losses due to the high value of materials and strict quality requirements.
3. Module Assembly: Battery packs require careful integration with connectors and control systems. Proper packaging and handling during this phase ensures flexibility for final assembly while maintaining optimal safety standards throughout production lines.
4. Packing & Final Distribution: Typically occurring near vehicle assembly points, this final stage involves transporting complete battery systems to overseas manufacturing facilities and aftermarket destinations. Efficient logistics solutions here directly impact production schedules and customer satisfaction.
The Growing Importance of Reverse Logistics
Beyond traditional supply chain management, battery manufacturers must now address reverse logistics—the transportation of damaged and used batteries to recycling and refurbishment centers across Asia, Europe, and North America. This circular approach maximizes resource utilization while complying with increasingly stringent environmental regulations.
By optimizing cost controls, inventory management, and logistics networks throughout this entire ecosystem, companies can significantly enhance profitability while building customer loyalty in this competitive market.
Meeting Tomorrow's Challenges Today
With decades of automotive supply chain expertise, industry leaders are developing battery logistics solutions that combine reliability, responsiveness, and flexibility. From precision inventory management to innovative transportation methods, these capabilities will prove essential as the EV revolution accelerates.
The road ahead is clear: only those manufacturers with robust, future-ready logistics strategies will thrive in the rapidly evolving landscape of electric mobility and battery technology.