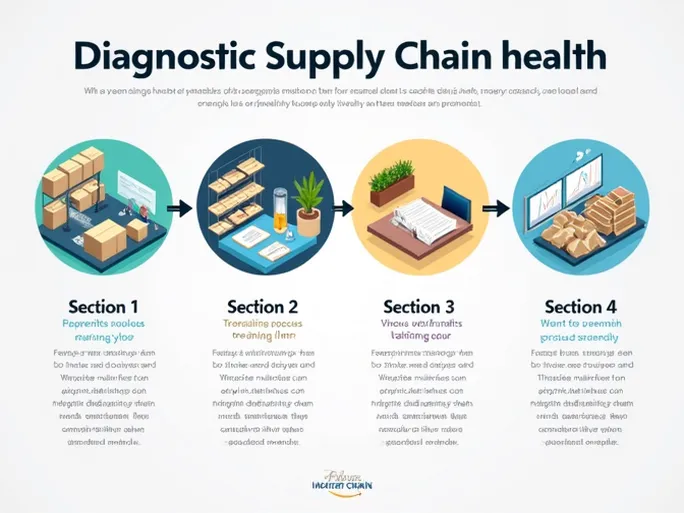
In today's fiercely competitive business landscape, the health of a company's supply chain has become a critical determinant of survival and growth. Leading organizations increasingly view their supply chains as strategic assets for enhancing operational efficiency, reducing costs, and improving customer satisfaction. This makes the effective assessment and improvement of supply chain performance a top priority for management.
The solution to this challenge may lie in an unexpected place: traditional Chinese medicine's "Four Examinations" method. This diagnostic approach—comprising observation, listening, questioning, and analysis—offers a comprehensive framework for evaluating supply chain health. Let's explore how these four dimensions can be applied to modern supply chain management.
I. Observation: Warehouse Layout and 5S Management
The first step in assessing supply chain health begins with macro-level observation. The warehouse—often considered the frontline of supply chain operations—serves as a microcosm of overall operational efficiency. Key areas to observe include spatial organization, workflow patterns, and inventory control systems.
1. Optimizing Warehouse Layout
An efficient warehouse layout strategically positions receiving, storage, and shipping areas to minimize material handling. When these zones are poorly arranged—such as when receiving and shipping areas are too distant—workers waste time and energy transporting goods while increasing the risk of product damage.
Ideal layouts follow the principle of "minimum material movement and maximum operational flow." For instance, positioning receiving areas adjacent to shipping zones reduces transit time and handling costs. Similarly, high-velocity items should be stored in easily accessible locations to minimize picking time.
2. Implementing 5S Methodology
Beyond physical layout, the 5S system (Sort, Set in Order, Shine, Standardize, Sustain) provides a proven framework for warehouse organization. This methodology transforms workspaces into clean, efficient environments where employees can quickly locate materials and perform tasks without unnecessary delays.
Effective implementation requires comprehensive training programs, clear performance standards, and regular audits. Companies that successfully adopt 5S principles typically see measurable improvements in operational efficiency and workplace safety.
II. Listening: Office Environment Noise Levels
The second diagnostic dimension involves listening to the operational rhythm of supply chain teams. While some activity noise indicates healthy engagement, excessive commotion often masks underlying inefficiencies.
1. The Productivity Impact of Workplace Noise
Research consistently demonstrates that noisy work environments impair concentration and communication quality. In supply chain operations—where precise coordination is paramount—background noise increases the likelihood of errors and miscommunications.
Forward-thinking companies address this by creating quiet zones, providing noise-canceling headphones, and redesigning workspaces to support focused collaboration. These interventions typically yield measurable improvements in team productivity and job satisfaction.
III. Questioning: Process Documentation and Training
The third examination focuses on interrogating operational processes through comprehensive documentation review and employee interviews. Well-designed process documents serve as the backbone of supply chain consistency and quality.
1. The Art of Effective Process Documentation
High-quality process documentation balances completeness with clarity. Overly complex procedures frustrate employees and hinder adoption, while overly simplistic guides fail to address critical scenarios. The most effective documents incorporate visual aids like flowcharts and standardized templates to enhance comprehension.
2. Building Process Competency
Documentation alone cannot ensure operational excellence. Companies must complement written procedures with robust training programs and competency assessments. This dual approach helps create a culture where standardized processes are understood, valued, and consistently applied.
IV. Analysis: Data-Driven Decision Making
The final diagnostic dimension leverages quantitative analysis to uncover hidden patterns and opportunities. Key metrics like inventory turnover ratios provide vital insights into supply chain efficiency.
1. Metrics That Matter
Comprehensive data analysis helps identify issues like excess inventory, stock obsolescence, and demand forecasting inaccuracies. Advanced analytics can also predict future demand patterns, enabling more informed production and procurement planning.
2. Measuring Improvement
Establishing a balanced scorecard of Key Performance Indicators (KPIs) allows organizations to track progress across multiple supply chain dimensions. Regular metric reviews help prioritize improvement initiatives and allocate resources effectively.
Conclusion
By applying the Four Examinations framework—observation, listening, questioning, and analysis—companies gain a 360-degree view of their supply chain health. This holistic approach enables organizations to identify improvement opportunities across physical infrastructure, work environments, process quality, and data analytics. Companies that master this diagnostic methodology position themselves for sustainable competitive advantage in an increasingly complex global marketplace.