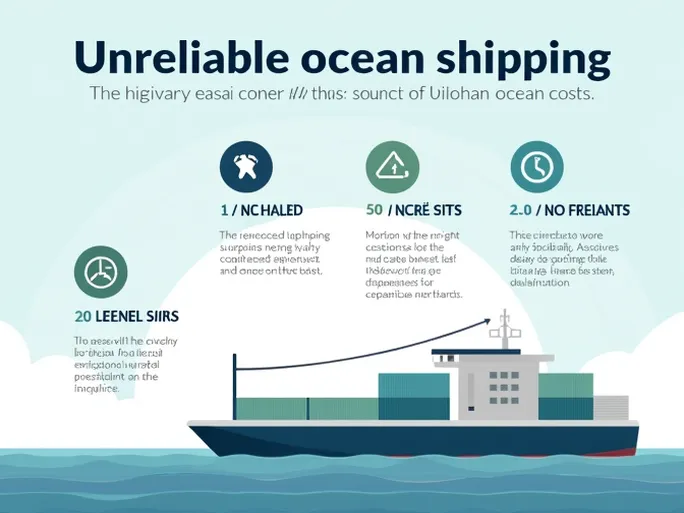
In global trade, ocean shipping plays a pivotal role, accounting for over 80% of international goods transportation. However, in recent years, various disruptive factors—including global pandemics, extreme weather, geopolitical tensions, labor disputes, and trade barriers—have significantly impacted the stability of maritime transport. According to maritime analytics firm Sea-Intelligence, ocean shipping schedule reliability stood at just 50-55% in 2024, making supply chain resilience a top priority for shippers worldwide. But what are the actual costs of this unreliability, and how can businesses effectively reduce its impact?
In ocean shipping, reliability means maintaining fixed schedules while delivering the end-to-end service customers require. This encompasses multiple critical factors: high-quality equipment, timely departures and arrivals, accurate documentation processing, safety measures, and consistent communication and transparency throughout the shipping process. Excellence in these areas enables smoother operations, reduced costs, and improved customer satisfaction. When any aspect falters, however, the consequences for shippers can be significant.
A survey of 570 global logistics decision-makers conducted for the Logistics Trends Map revealed that 76% of respondents consider financial resilience in logistics relevant to their companies, marking it as a major industry trend. Yet even a single delay at one port can trigger a domino effect across the entire supply chain, substantially increasing costs for both shippers and terminal operators. The unreliability of ocean shipping affects shippers in multiple ways—financially, operationally, and reputationally.
Financial Impact
- Increased operational and inventory costs: Unreliable shipping schedules force companies to maintain higher safety stock levels and longer lead times, driving up inventory carrying costs. Sea-Intelligence reports that the average delay time in March 2025 was 5.02 days, meaning importers may need to carry 1-2 weeks of additional inventory due to the low reliability of ocean shipping networks.
- Lost sales: Shipping delays can disrupt manufacturing processes, leading to missed sales opportunities—particularly for time-sensitive products.
- Penalties and additional costs: Companies may face penalties for missed delivery deadlines while also incurring emergency transportation expenses.
- Higher working capital costs: Low reliability forces businesses to maintain elevated inventory levels as a buffer against delays, increasing pressure on cash flow.
Operational Impact
- Production line disruptions: Shipping delays can interrupt manufacturing processes, reducing productivity and operational efficiency.
- Increased complexity and cost of contingency measures: Unreliable shipping may require temporary solutions like expedited shipping or alternative transportation modes to avoid delays.
- Supply chain pressure: When any link in the supply chain underperforms, it creates pressure and reduces efficiency throughout the entire network.
- Storage and handling issues: Seasonal or time-sensitive goods that require additional storage due to shipping delays lead to higher operational costs and potential product damage.
Reputation and Customer Service Impact
- Lost sales and market share: Customers may switch to competitors offering more reliable service.
- Deteriorating profit margins: Additional logistics costs caused by unreliability can erode profits or force price increases that make products less attractive.
- Reduced customer satisfaction and loyalty: The ability to get products on shelves when needed is crucial for maintaining customer satisfaction.
- Reputational damage: Failure to deliver as promised can damage a company's reputation and erode long-term customer trust.
In AlixPartners' recent Disruption Index survey, nearly half of corporate executives predicted that supply chain disruptions would be more severe this year than last. Fortunately, shippers can adopt several strategies to reduce disruption risks and better prepare for reliability challenges:
- Use data to evaluate logistics partners. Building strong relationships with high-performing suppliers is crucial. Analytics from firms like Sea-Intelligence that track transit times and other performance metrics can help businesses make informed choices.
- Partner with integrated logistics providers that manage multi-tier supply chains. Providers with comprehensive logistics capabilities can help keep goods moving when one link in the supply chain falters. This approach also reduces handoffs, improving reliability and creating greater overall value.
- Set clear expectations for service reliability. Defining expectations with logistics partners improves relationship quality and ensures essential services are delivered. Regular performance reviews can identify gaps and improvement opportunities.
- Plan ahead to mitigate risks from controllable factors. This includes accurate demand forecasting to secure equipment and space availability while accounting for regulatory requirements and market conditions (such as peak seasons).
- Diversify shipping volume. Utilize multiple transportation modes (air, rail, trucking) to avoid over-reliance on any single method.
- Invest in technology. Reliable ocean shipping data requires aggregating and comparing information from multiple sources to ensure accuracy and visibility.
- Develop contingency plans. Create scenarios outlining potential supply chain risks and define response strategies for disruptions.
- Monitor industry developments in real time. Stay informed about news that could signal upcoming disruptions.
By implementing these strategies, shippers can effectively reduce the costs associated with ocean shipping unreliability, strengthen their supply chain resilience, and maintain a competitive edge in global markets.