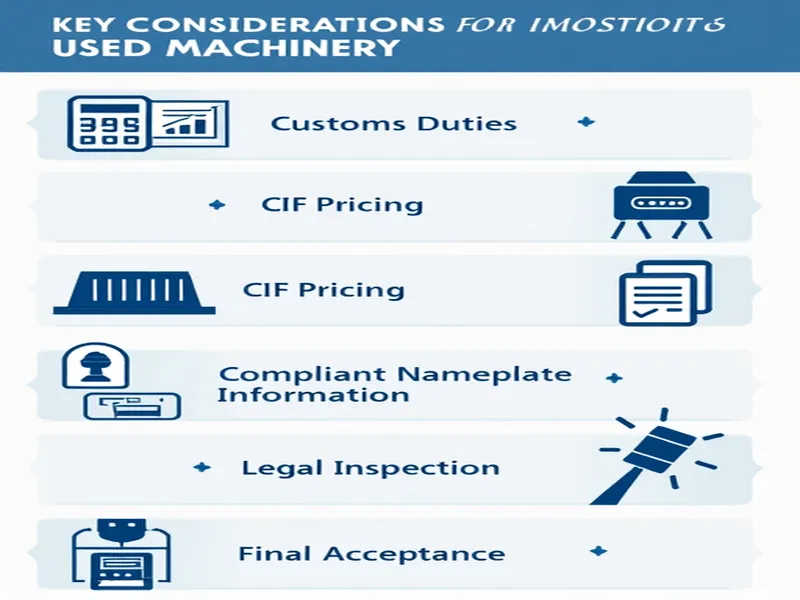
In today's rapidly evolving global economy, an increasing number of companies are considering importing complete sets of machinery equipment to enhance production efficiency and technological capabilities. However, the import process is far from straightforward, involving numerous legal regulations, customs procedures, and tax considerations. Understanding the critical details in importing complete machinery equipment has become essential.
Taxation: A Key Financial Consideration
For importers, customs duties and value-added taxes represent crucial financial factors. In China, complete machinery equipment currently carries an 8% tariff rate with an additional 13% VAT. These rates may vary for different types of equipment, making it imperative to consult tax experts before purchasing to ensure accurate cost projections. Tax variations can directly impact project budgets and investment decisions.
Accuracy in Customs Declarations
Beyond taxation, the accuracy of declared CIF prices (cost, insurance, and freight) and customs codes significantly affects the import process. Many importers face customs challenges due to inaccurate pricing or classification. In such cases, importers should prepare supporting documents including letters of credit, purchase contracts, and invoices to facilitate smoother customs clearance.
Customs authorities particularly scrutinize equipment nameplate information during document verification. Importers must ensure consistency between nameplate details and declaration materials to avoid unnecessary delays. Many companies now request suppliers to provide clear, authentic nameplate photographs during procurement to simplify later declarations.
Regulatory Compliance and Inspection
During transportation, equipment may undergo legal inspections focusing on quality, safety, and environmental compliance standards. These inspections typically follow customs quarantine procedures. Importantly, equipment must be assembled and tested at the operational site after passing inspections—a critical step affecting both functionality and final acceptance.
Final Approval and Operational Readiness
Before operational use, equipment must pass final inspection by local customs authorities. Failure to meet standards risks rendering equipment unusable and may result in financial penalties. Companies must therefore thoroughly understand and comply with relevant regulations at every import stage to ensure successful clearance and operational deployment.
The process of importing complete machinery equipment presents numerous complexities and requires meticulous attention to detail. To streamline operations, companies should prepare thoroughly and maintain close collaboration with specialized import agencies or legal advisors. Only through such diligence can businesses successfully navigate this challenging process and seize competitive advantages in today's dynamic market environment.