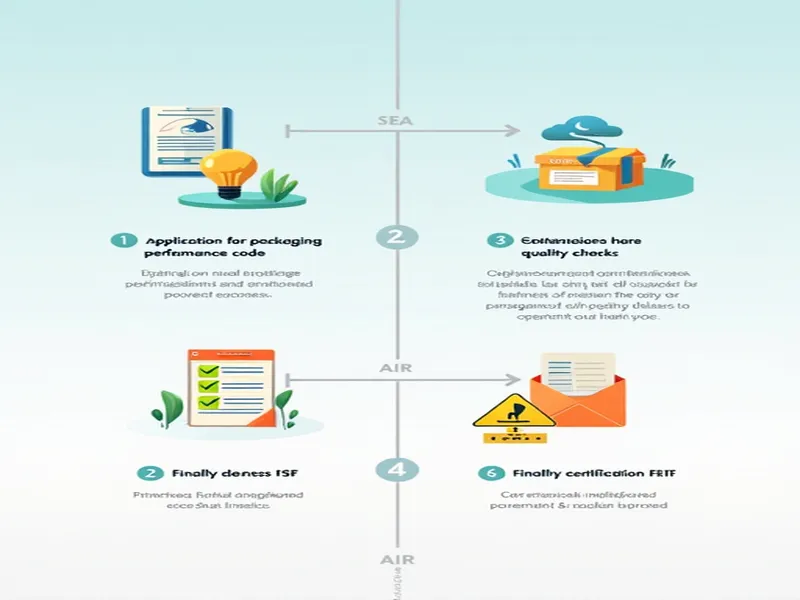
When exporting dangerous goods, obtaining proper packaging certification is a mandatory step. Whether shipping full container loads or less-than-container quantities, this certification is legally required for all hazardous material transports. There are two versions of the certification available — one for maritime shipping and another for air transport — as each mode has distinct safety standards and regulations.
The Certification Process
The first step in obtaining dangerous goods packaging certification involves securing a packaging performance report. This process consists of several critical components:
- Manufacturer Registration: Packaging container producers must apply for identification codes through their local customs authority to undergo performance testing. Customs officials supervise these export packaging manufacturers to ensure compliance with safety protocols.
- Marking Requirements: All export packaging must display the UN-mandated hazardous materials markings along with the manufacturer's identification code, maintaining transparency and traceability throughout the supply chain.
- Performance Testing: Regular inspections verify packaging integrity. Liquid containers undergo rigorous assessments including drop tests, stacking evaluations, leak-proof examinations, and hydraulic pressure checks. Solid material packaging, typically corrugated cardboard or woven plastic bags, must pass drop and stacking tests to demonstrate structural reliability.
Upon successful completion of all testing procedures, manufacturers receive the Entry-Exit Goods Packaging Performance Inspection Report . This document confirms the packaging's legal compliance and establishes the foundation for the final dangerous goods transport certification.