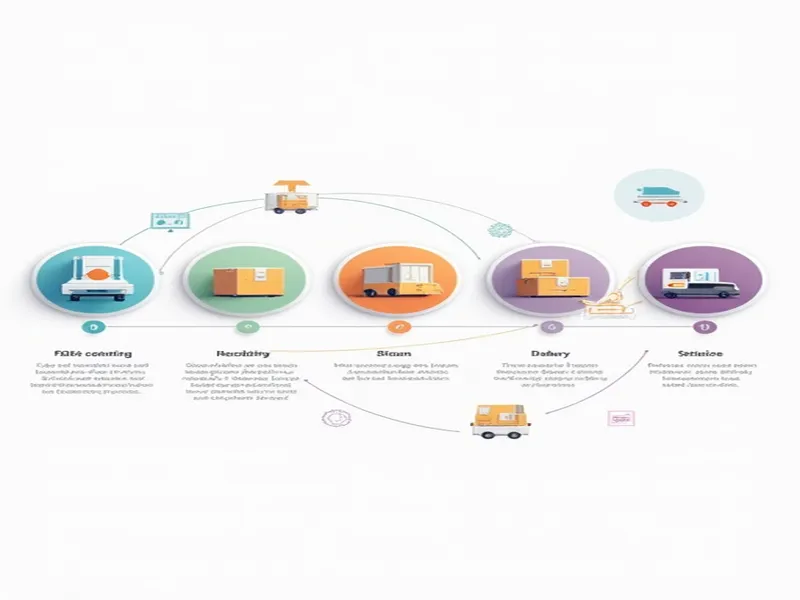
When preparing shipments for Amazon's Fulfillment by Amazon (FBA) program, ensuring products arrive safely and efficiently at Amazon warehouses requires strict adherence to specific procedures. FBA's core purpose is allowing sellers to focus on sales while delegating logistics and storage complexities to Amazon. Therefore, thoroughly understanding the shipping process and its details before dispatch becomes crucial.
Product Quantity Verification
First, verifying the exact shipping quantity for each product is essential. Before shipping, confirm that the quantity of every product matches the information entered in your Amazon seller account. This practice prevents inventory discrepancies and safeguards against potential sales disruptions. Accurate quantity records help avoid complications like refunds or inventory issues stemming from shipping errors.
Proper Labeling Procedures
Each item requires appropriate labeling:
- Use laser printers for clear, scannable labels
- Standard label sizes: 1"×2⅝" for product labels, 3⅓"×4" for package labels
- Ensure labels remain undamaged during transit—smudged or torn labels may cause scanning failures
When applying labels, reference Amazon's provided PDF documentation and attach labels individually to each product. Verify that product names exactly match label information to prevent warehouse confusion. Label accuracy affects both successful warehouse receipt and subsequent sales, as precise product information forms the foundation of customer satisfaction.
Container Labeling and Tracking
Beyond product labels, affix container labels (box ID labels) below carrier labels. This critical step enables both carriers and Amazon's system to identify shipment origins and quickly resolve transportation issues. Selecting carriers that provide tracking numbers is particularly important, allowing you to monitor shipment status at every stage and keeping Amazon informed of product locations—significantly enhancing supply chain transparency and efficiency.
Key Shipping Prohibitions
Several practices must be avoided to ensure smooth operations:
- Never omit labels unless you've established commingled inventory—missing labels may result in warehouse returns or unnecessary delays
- Avoid inkjet printers for labels—inkjet prints may lack durability and clarity during transit and storage
- Position labels carefully—avoid placing them near vulnerable edges where contact might cause damage
- Keep individual package weights under 50 pounds—exceeding this limit increases shipping costs and risks rejection
Additional Critical Considerations
Adhere strictly to the "no mixed shipments for different orders" rule. Shipping quantities must match system-entered data precisely, minimizing potential errors during Amazon's receiving process. Never exceed the declared shipment quantity online to prevent losses from shipping mistakes.
Finally, ensure new shipping boxes contain no remnants of previous shipments' packing slips. Such oversight might confuse warehouse staff and lead to inventory management errors. By following these detailed procedures and avoiding prohibited practices, you can establish smooth, secure FBA first-mile shipping processes that maximize your sales efficiency.