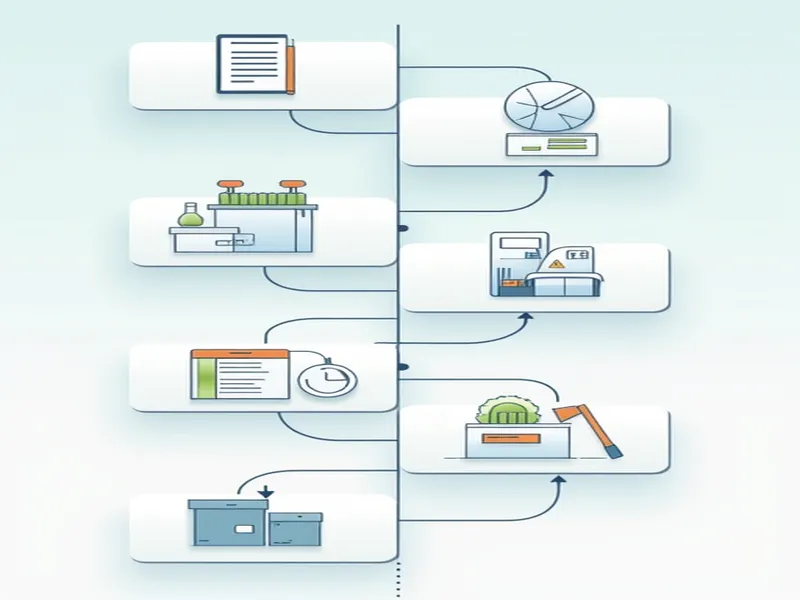
The warehouse inbound process involves several critical steps to ensure goods are properly received, inspected, and stored. Here's a detailed look at the standard procedure:
1. Initial Inspection and Packaging Check
Upon arrival at the warehouse, staff carefully examine the external packaging of all goods to identify any visible damage. When packaging defects are found, workers photograph the damage for documentation and immediately notify the client to arrange for repackaging, ensuring products remain protected throughout the storage period.
2. Sorting and Classification
Using the client-provided sorting list number, warehouse personnel systematically categorize the incoming goods. This meticulous sorting process significantly reduces the likelihood of errors in subsequent handling stages.
3. Security Screening
All sorted items undergo mandatory security screening through X-ray machines—a crucial safety measure that prevents prohibited items, flammable materials, and explosive substances from entering the storage facility. For items that cannot be properly identified by the scanning equipment, staff conduct manual box inspections.
4. Precise Measurement and Verification
Each item receives individual attention as workers record exact weight and dimensional measurements. When significant discrepancies are detected between actual measurements and provided specifications, staff document these variations with photographic evidence and promptly inform the client. After verification, goods are placed in designated locations ready for labeling and eventual outbound processing.
5. Claims Management Protocol
To properly handle client claims regarding lost or damaged goods, warehouse personnel maintain thorough knowledge of shipping companies' claims procedures and required documentation. This expertise ensures clients' rights and interests receive proper protection throughout any claims process.