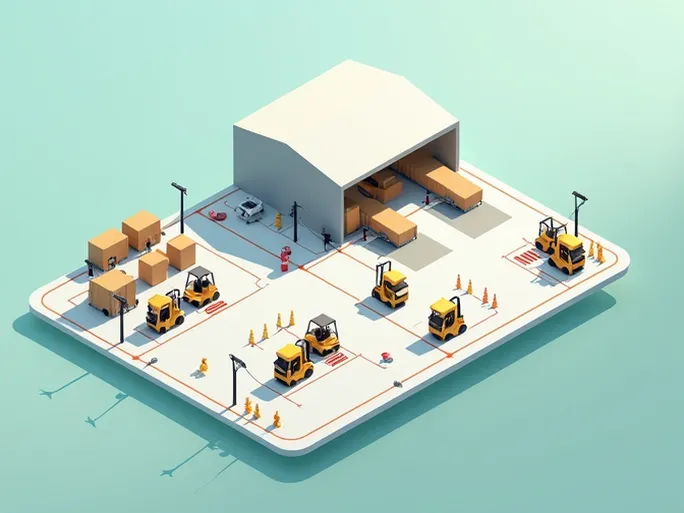
In today's rapidly evolving economic landscape, the warehousing and logistics industry has become a core component of operations across all sectors. With the increasing frequency of global trade, the safety and efficiency of loading and unloading operations have gained paramount importance. Effective loading management not only boosts operational efficiency but also directly impacts customer satisfaction and a company's market competitiveness. Consequently, more businesses are paying attention to every detail of loading operations, striving to minimize potential issues.
In warehouse logistics, loading and unloading operations serve as both the bridge for goods transportation and a critical safeguard for cargo security. Companies must develop systematic loading management protocols that rely not only on advanced technology but also comprehensive management across multiple aspects including staff training, equipment maintenance, and safe operations. This article explores various approaches to enhance safety and efficiency in warehouse loading operations, presenting a complete set of management measures.
I. Fundamental Requirements for Cargo Handling
Loading and unloading operations must adhere to core principles: safety first, gentle handling, stable stacking, and maintaining clear pathways. These fundamental requirements are crucial for daily warehouse management and serve as effective defenses against accidents and employee injuries.
1. Onboarding Training and Skill Development
In any organization, employee training forms the foundation for efficiency and safety. Logistics companies must provide comprehensive training for all loading staff, covering warehouse layout, equipment usage, and safety protocols. Proper training enhances productivity while reducing errors and accidents caused by unfamiliarity with procedures. Training should include basic operational knowledge and specialized equipment maintenance techniques, reinforced through regular drills and assessments.
2. Equipment Usage and Maintenance
Modern warehouse management requires careful attention to loading equipment such as forklifts, hand trucks, and conveyor belts. Forklifts are essential for heavy loads while hand trucks suit smaller items. Regular maintenance and inspections ensure equipment reliability. Forklift operators should possess basic troubleshooting skills to handle emergencies. Selecting appropriate tools for different cargo types maximizes efficiency.
Beyond operator training, companies must implement daily equipment management systems with scheduled inspections to maintain readiness. This extends equipment lifespan and reduces safety risks from malfunctions.
3. The Critical Importance of Safe Operations
Safety is the top priority in loading operations. Forklift activities require designated spotters to prevent bystander accidents. Operators must remain vigilant during transport to prevent cargo shifts or falls, promptly addressing potential hazards.
Companies should cultivate safety awareness through regular training and drills, ensuring all employees understand emergency response procedures. This preparedness minimizes damage and injuries during critical situations.
4. Special Handling for Fragile Goods
Warehouses handle diverse cargo types requiring special attention for fragile, damage-prone, or high-value items. Protective measures include cushioning materials, gentle handling, reinforced packaging with bubble wrap or wooden crates to minimize impact damage. For valuable goods, reducing unnecessary handling lowers risk exposure.
5. Responding to Quality Defects
When quality issues are detected during unloading, immediate action is required. All loading personnel should receive training in cargo inspection to identify and categorize problems, especially after long-distance or maritime transport where environmental factors may cause damage. Vigilant inspection protocols and prompt reporting prevent customer complaints and claims.
II. Safety Protocols for Loading Operations
To enhance safety, companies must establish clear operational standards enforced across all employees. Detailed safety procedures significantly reduce risks to personnel and cargo integrity.
1. Unloading Precautions
During unloading, open truck doors cautiously to prevent falling cargo. Heavy items require team lifting with proper weight distribution. Coordinated movements ensure optimal safety.
2. Bulk Cargo Management
Different bulk materials require specialized equipment like conveyors for grains or fertilizers, reducing manual labor and hazards. Proper storage and stacking ensure stability during handling.
3. Packaging Standards
Select packaging based on cargo characteristics: wooden crates for heavy items, multi-layer cushioning for fragile goods. Ensure neat stacking without overloading to guarantee transport safety.
4. Hazardous Materials Procedures
Comply with all regulations for hazardous goods transport, including classification, clear labeling, and specialized handling by trained personnel. All staff must understand material properties through dedicated training.
5. Loading Sequence Techniques
Follow "heavy not over light" and "large not over small" stacking principles. Mark fragile items clearly and assign dedicated monitors throughout transit.
III. Post-Operation Procedures and Review
After completing loading tasks, thorough site organization ensures subsequent operations proceed smoothly. Key steps include:
- Clearing workspaces and properly storing tools
- Conducting regular equipment maintenance checks
- Debriefing teams to analyze successes and improvement areas
This systematic approach identifies and eliminates potential risks while reinforcing safety awareness among all personnel.
Conclusion
The logistics industry plays an irreplaceable role in the modern economy. As companies pursue greater efficiency and cost control, optimizing loading operations has become a critical challenge. Implementing robust loading management systems enhances operational efficiency, reduces labor intensity, and ensures safe working environments. Through continuous innovation and process improvement, logistics firms can achieve higher standards in both safety and productivity.
Developing systematic, efficient loading procedures is essential for competitive advantage. By investing in modern technology and workforce training, logistics companies can deliver superior service while advancing industry standards, ultimately contributing to the sustainable growth of the warehousing and logistics sector.