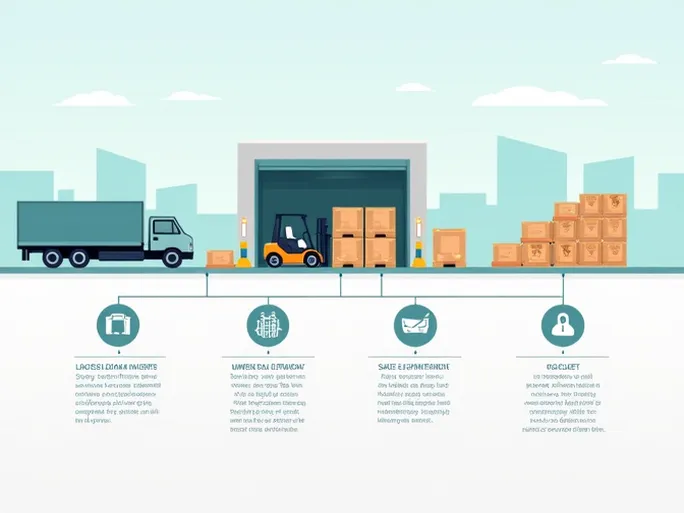
In today's increasingly competitive logistics industry, the safety and efficiency of loading and unloading operations have become crucial components of corporate competitiveness. Efficient and safe loading processes not only enhance operational productivity but also significantly reduce cargo damage rates, thereby improving customer trust and satisfaction. This article provides an in-depth exploration from multiple perspectives, offering a systematic approach to loading operations that can help logistics companies improve their practical efficiency.
I. The Significance and Importance of Loading Operations
Loading operations are a critical link in the logistics system, involving the transfer of goods from transportation vehicles to storage facilities or vice versa. Effective loading not only concerns the safety and integrity of goods but also directly impacts the efficiency of the entire logistics chain. To understand the importance of loading processes, we can analyze the following aspects:
- Enhancing Work Efficiency: Efficient loading processes can significantly reduce cargo waiting time, thereby improving productivity and meeting customer demands for timeliness.
- Reducing Cargo Damage Rates: In busy loading environments, improper operations can easily lead to cargo damage, loss, or misplacement. Standardized loading procedures can effectively minimize such losses.
- Optimizing Human Resource Allocation: By properly planning staff responsibilities, companies can maximize each employee's capabilities, leading to better resource utilization.
- Ensuring Personnel Safety: Loading operations present various potential hazards. Standardized procedures can effectively prevent accidents and protect worker safety.
II. Basic Requirements for Cargo Loading
Before undertaking loading operations, understanding fundamental requirements is essential. The following principles should guide the implementation process:
- Safety First, Handle With Care: Safety remains the top priority throughout the loading process. Both equipment operation and cargo handling require high vigilance.
- Stable Stacking, Clear Pathways: Proper stacking maintains cargo integrity while ensuring efficient movement within the workspace through accessible pathways.
- Horizontal and Vertical Alignment: Establish clear arrangement patterns to facilitate quick cargo identification and improve efficiency.
- Labels Outward, Arrows Up: Cargo labels should face outward to prevent unnecessary handling that might damage them, with directional arrows pointing upward to avoid inversion.
- Large Over Small, Heavy Over Light, Damaged Over Intact: Follow proper weight and volume distribution to protect smaller, lighter items from being crushed by heavier ones.
- Wood Not Over Paper, Square Not Over Round, Dry and Wet Separated: For different cargo types, prevent mutual damage by keeping incompatible items separate, especially dry and wet goods to avoid contamination.
III. Systematic Loading Operation Procedures
The following recommended loading system procedures aim to enhance efficiency and safety through standardization:
1. Area Division and Responsibility Assignment
Before loading begins, clearly define warehouse zones and corresponding responsibilities. Consider:
- Functional Areas: Receiving, shipping, storage, etc.
- Cargo Characteristics: Separate fragile items, liquid goods, etc., from regular cargo.
2. Labeling and Zone Management
Use color coding and labeling systems to classify different cargo types and customer shipments for quick, accurate operations. Clearly mark environmental requirements (temperature, humidity) for storage areas.
3. Equipment Operation and Maintenance
Various handling equipment (forklifts, hand trucks, etc.) require proper use and regular maintenance. Maintain usage and maintenance logs for performance analysis.
4. Forklift Safety Operations
Forklift operators must receive regular safety training and adhere to:
- Load Limits: Never exceed rated capacity
- Speed Control: Maintain low speeds in warehouse areas
- Avoid Tilt Operations: Prevent tilting when handling high stacks
5. Loading Techniques
When using hand trucks, avoid forcing them under stacks. Handle fragile items (glass, etc.) with extra care and special labeling.
6. Cargo Protection and Exception Handling
Implement detailed protection measures for fragile goods. Report and document any abnormalities for future improvement.
7. Loading Vehicle Considerations
Design loading plans based on cargo characteristics:
- Valuable Items Center-Placed: Position in truck center for stability
- Balanced Weight Distribution: Ensure even placement to prevent driver discomfort and safety hazards
8. Workspace Cleanliness and Tool Management
After operations, promptly clean the area (remove debris, dust) and return all tools to designated locations.
9. Daily Safety Supervision
Establish safety teams to monitor operations, conduct regular inspections, and implement continuous improvement through feedback and performance evaluations.
10. Safety Precautions
Maintain constant vigilance: open truck doors slowly to prevent cargo falls; use proper safety gear (harnesses, etc.) for elevated work.
IV. Data Analytics in Loading Operations
Modern logistics increasingly employs data analysis to identify and address operational challenges:
- Efficiency Metrics: Record loading times to identify bottlenecks and optimize workflows
- Damage Rate Analysis: Track damage incidents to determine root causes for risk management and training
- Performance Evaluation: Assess staff productivity for optimal task and resource allocation
- Equipment Utilization: Analyze usage frequency and maintenance records for timely servicing
Conclusion
In logistics, loading operations represent a complex yet vital link directly impacting customer experience and corporate efficiency. Through standardized, systematic procedures, companies can enhance operational productivity while building greater customer satisfaction and trust. By implementing the guidelines outlined above, logistics firms can optimize management practices and strengthen market competitiveness. While loading may appear simple, it involves specialized knowledge and techniques—only through meticulous management and practice can operations achieve both safety and efficiency.