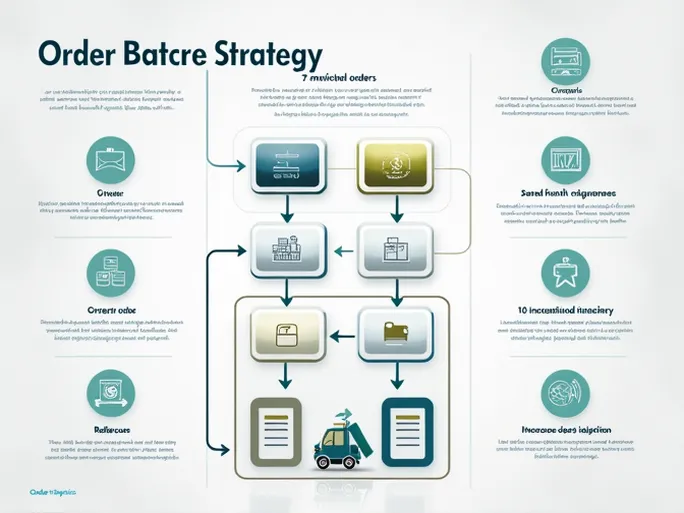
In today's fast-paced e-commerce and logistics industry, improving order fulfillment efficiency remains a critical challenge for businesses. As consumer expectations for rapid delivery continue to rise, companies must constantly enhance their order processing capabilities to meet growing demand. During peak seasons, many businesses face issues with excessive warehouse staff movement and order processing delays—problems that not only extend delivery times but also impact customer satisfaction and damage corporate reputation.
In this context, logistics order batching strategies have emerged as a powerful solution to boost warehouse operational efficiency. The core concept of order batching involves consolidating multiple orders into batches for unified processing. This approach enables warehouse staff to minimize travel time, optimize picking routes, and increase order throughput per work hour.
I. THE FUNDAMENTALS OF ORDER BATCHING
The principle behind order batching is simple yet effective. Traditional order processing typically involves picking items for each order individually, resulting in redundant routes and wasted time. Order batching aggregates multiple orders based on shared picking paths and timing. For example, when two customers order the same product, warehouse staff can retrieve the item once to fulfill both orders simultaneously—reducing time spent and lowering labor costs.
II. KEY BENEFITS OF BATCH PROCESSING
- Enhanced Efficiency: Reduced travel time allows staff to process more orders within the same timeframe.
- Optimized Space Utilization: Batching enables more efficient warehouse space usage while minimizing unnecessary inventory buildup.
- Improved Accuracy: Processing similar orders collectively reduces error risks and ensures accurate deliveries.
- Cost Savings: Streamlined picking routes and reduced labor intensity lower operational expenses.
- Superior Customer Experience: Faster, more accurate order processing significantly boosts satisfaction and encourages repeat purchases.
III. CRITICAL IMPLEMENTATION FACTORS
When adopting order batching, businesses must focus on several key aspects. First, thorough analysis of order data helps identify patterns for consolidation and develop precise batching strategies. This requires comprehensive statistical analysis to understand order commonalities.
Second, warehouse physical layout significantly impacts effectiveness. Optimal designs considering product categories, shelf heights, and picker routes ensure efficient batch processing with minimal travel distance.
Additionally, proper workforce allocation and skill assessment dramatically improve efficiency. Regular training ensures staff mastery of new technologies and processes, enhancing overall team performance.
IV. HIGH-EFFICIENCY BATCHING STRATEGIES
Businesses can implement these proven batching approaches:
- Scheduled Picking: Group orders by cutoff times or product similarities to optimize execution.
- Zone-Based Picking: Divide warehouses into designated areas with dedicated staff to minimize interference and movement.
- Collaborative Picking: Enable pickers to simultaneously retrieve items for multiple matching orders.
- Dynamic Hybrid Picking: Flexibly adjust strategies based on real-time order characteristics, inventory status, and workforce availability.
V. CHALLENGES AND SOLUTIONS
While order batching offers significant advantages, implementation presents challenges. System upgrades may cause initial disruptions, requiring comprehensive staff training for smooth transitions. Precise coordination is particularly crucial in time-sensitive sectors like pharmaceuticals to prevent delivery delays.
During peak periods, businesses should dynamically adjust batch sizes to accommodate fluctuating order volumes, preventing processing slowdowns and errors from oversized batches. Continuous optimization of allocation strategies is essential.
VI. STEPS TO SUCCESSFUL IMPLEMENTATION
Effective order batching requires these key steps:
- Process evaluation and bottleneck identification through time-motion studies
- Comprehensive order characteristic analysis to design appropriate batching strategies
- Workforce capacity assessment and optimal staff allocation
- Strategy selection based on warehouse layout and order patterns
- Seamless Warehouse Management System (WMS) integration
- Automation of repetitive, labor-intensive tasks
- Pilot testing with continuous performance monitoring and adjustment
- Comprehensive team training and development of continuous improvement culture
VII. CONCLUSION
By following these guidelines, businesses can successfully implement order batching strategies to dramatically improve warehouse efficiency and order accuracy—securing competitive advantage in today's demanding e-commerce landscape. Companies must move beyond traditional approaches and embrace innovative technologies and methodologies to achieve sustained performance improvements and customer satisfaction. In the rapidly evolving logistics sector, flexible, efficient order processing systems are becoming the cornerstone of business success. Achieving this requires scientific management strategies, team collaboration, and comprehensive technological support. Through continuous optimization, organizations can better adapt to market changes, enhance customer experiences, and reach higher business objectives.